The CNC press brake machine (Computer Numerical Control press brake) is one of the essential pieces of equipment in modern metalworking industries. It is widely used for bending various metal sheets and can accurately complete bending tasks of different angles and shapes. With advancements in technology, CNC press brake machines have become more powerful and easier to operate, making them a core piece of equipment on many production lines.
CNC Press Brake Machines
A CNC press brake machine uses computer numerical control technology to precisely control parameters such as bending angle, bending position, and upper die pressure depth. Compared to traditional press brake machines, CNC press brakes not only significantly improve processing accuracy but also can complete complex bending tasks in a shorter time, greatly enhancing production efficiency.
The main components of this equipment include: CNC system, hydraulic system, mechanical drive parts, work table, and dies. By setting parameters on the control interface, users can easily meet the processing requirements for various metal materials. CNC press brake machines are widely used in industries such as metalworking, aerospace, automotive manufacturing, and construction.
CNC Press Brake Machine Use Steps
When using a CNC press brake machine for processing, it is essential to follow the operating steps to ensure precision and safety. Below is a general process for using a CNC press brake machine:
-
Preparation:
- Inspect the Machine: Before starting, check all components of the machine to ensure that the hydraulic, pneumatic, and transmission systems are functioning properly.
- Select the Die: Choose the appropriate upper and lower dies according to the thickness and bending requirements of the material and ensure they are securely installed.
- Place the Material: Position the metal sheet to be processed on the work table, ensuring that the material is flat and free of defects.
-
Set Parameters:
- Input parameters such as bending angle, length, and bending depth according to the specific requirements of the workpiece. These settings will determine the bending precision and final results.
- Set appropriate bending speed and pressure to ensure that the material is not deformed or damaged during the process.
-
Trial Bending:
- Before starting formal processing, it is advisable to conduct a trial bend to ensure that the set parameters are correct and verify the compatibility of the dies, avoiding errors.
-
Formal Bending:
- Start the machine to perform the official bending operation. During operation, ensure to maintain a safe distance to avoid accidents.
-
Check the Finished Product:
- After processing, thoroughly inspect each workpiece to ensure the bending angle and dimensions meet the desired specifications. If any deviation is found, adjust the parameters and reprocess the part.
CNC Press Brake Machine Precautions
To ensure the high-efficiency operation and precision of CNC press brake machine, operators should pay attention to the following aspects:
-
Safety Operations:
- Wear Protective Equipment: Operators must wear appropriate safety gear such as safety glasses and gloves to prevent accidents.
- Follow Operating Procedures: Before operating the CNC press brake, familiarize yourself with the machine’s user manual and adhere to safety standards. Ensure that each operator has received professional training and possesses the necessary operational skills.
- Prevent Foreign Object Interference: Keep the operating area clean and free of debris to prevent foreign objects from entering the machine, avoiding faults or accidents.
-
Equipment Maintenance and Care:
- Regular Inspections and Maintenance: Periodically check the levels of hydraulic oil, lubrication oil, and other fluids to ensure the proper operation of the hydraulic system and mechanical parts. Inspect the dies for wear and replace them as necessary.
- Keep Clean: Clean the work table and dies regularly to avoid the accumulation of metal chips or other debris that could interfere with machine operation.
-
Proper Material Selection:
- Choose the right material according to the processing requirements. The thickness, hardness, and other factors of the metal sheet directly impact the bending effect and the required pressure.
- Check the Material Status: Before processing, ensure that the material is free of cracks, defects, and that its surface is flat and free of oil stains.
-
Importance of Parameter Settings:
- The accuracy of the CNC press brake machine operation is closely related to the parameter settings. When inputting parameters, adjust them based on the type, thickness, and bending angle of the material.
- Excessive pressure or incorrect bending angles may cause material rupture or equipment damage, affecting production efficiency.
-
Avoid Overloading:
- To extend the life of the equipment, avoid overloading during operation. Overburdening the machine can cause significant damage, leading to equipment failure.
Conclusion
The CNC press brake is an indispensable piece of high-precision equipment in modern manufacturing. By utilizing numerical control technology, it achieves efficient processing of metal sheets. Proper use of the CNC press brake machine not only improves work efficiency but also ensures processing precision and quality. However, safety during operation, regular maintenance, and proper parameter settings are crucial. By adhering to strict operating procedures and maintenance practices, CNC press brake machines can operate stably over the long term, providing enterprises with greater production efficiency.
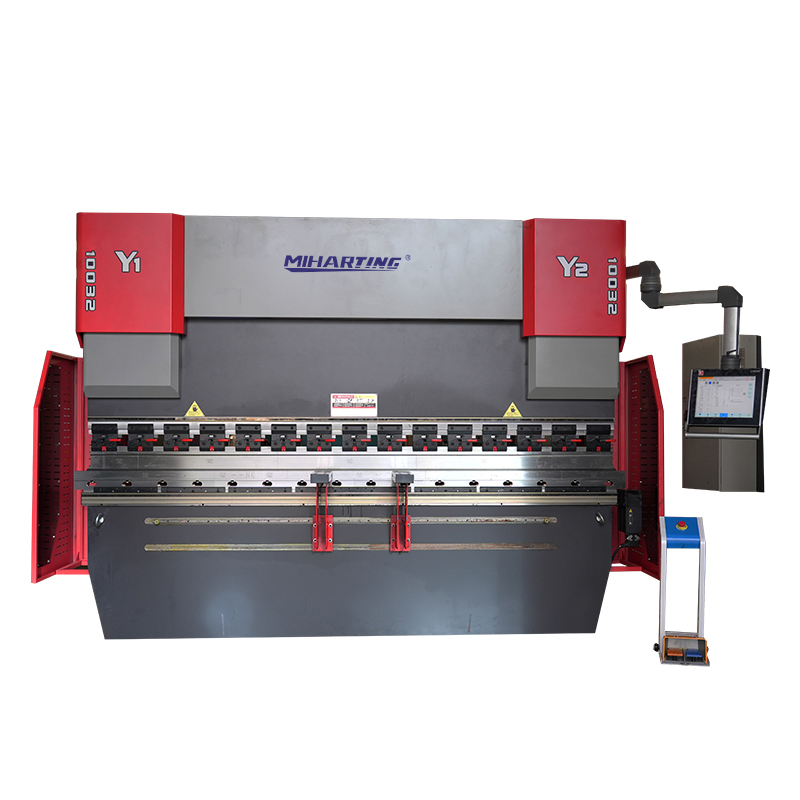
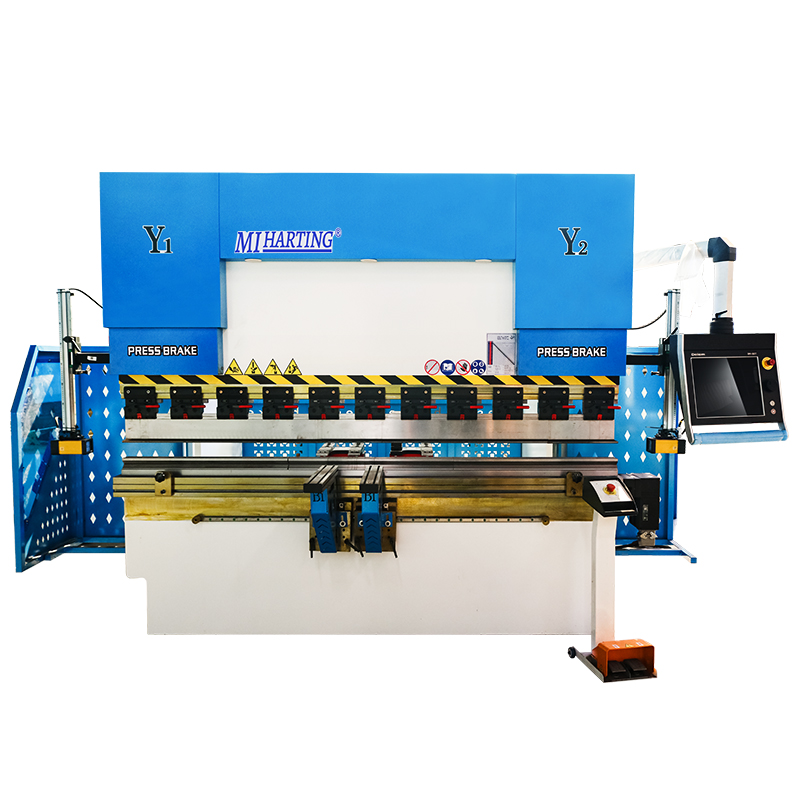