1.press brake machine High rigidity body and foundation design
●Adopt gantry or C-shaped body structure, optimize the force distribution of the body through finite element analysis, and adopt high-strength cast iron or welded steel structure to ensure overall rigidity and deformation resistance.
●Priority layout function expansion, such as backgauge (X-axis), closest stroke (Y-axis), mechanical compensation (W-axis) and other modules are independently adjustable to adapt to different processing needs.
2. Servo drive and multi-axis linkage control
The core power uses a servo motor to directly drive the ball screw or hydraulic servo system to achieve high response speed of the X/Y axis (the X axis can reach 6m/min, and the Y axis positioning accuracy is ±0.005mm).
●Supports 4+1 axis (Y1/Y2/R/X/W axis) synchronous control, and realizes multi-axis interpolation operation through PLC and EM253 positioning module to ensure the accuracy of complex bending trajectories
3. Intelligent compensation system
● Integrated hydraulic crown compensation or mechanical deflection compensation device, dynamically adjusts the deflection of the workbench through real-time monitoring of plate deformation, compensates for elastic deformation during the bending process, and ensures the consistency of the bending angle throughout the entire length.
4. Human-computer interaction interface
● Equipped with a high-resolution touch screen , which supports graphical programming, process parameter preset and bending process simulation, reducing operational complexity.
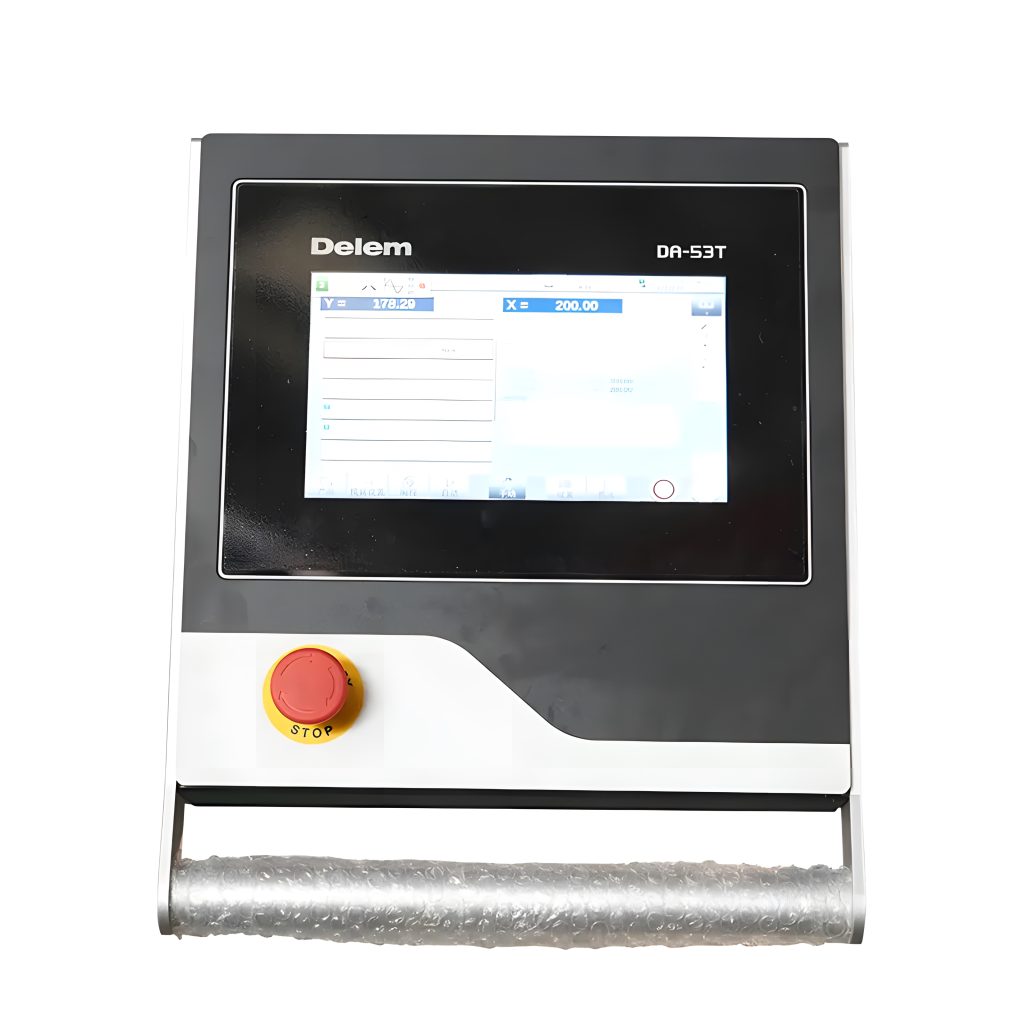
•"Shortcut" touch navigation. 10.1" high-definition TFT display •Multiple 4-axis control •Deflection compensation control •With mold/material/product library •Support servo or frequency conversion control •Advanced X-axis control method can control both loop adjustment and open-loop false adjustment. •Network dual-machine linkage (optional) •USB peripheral interface
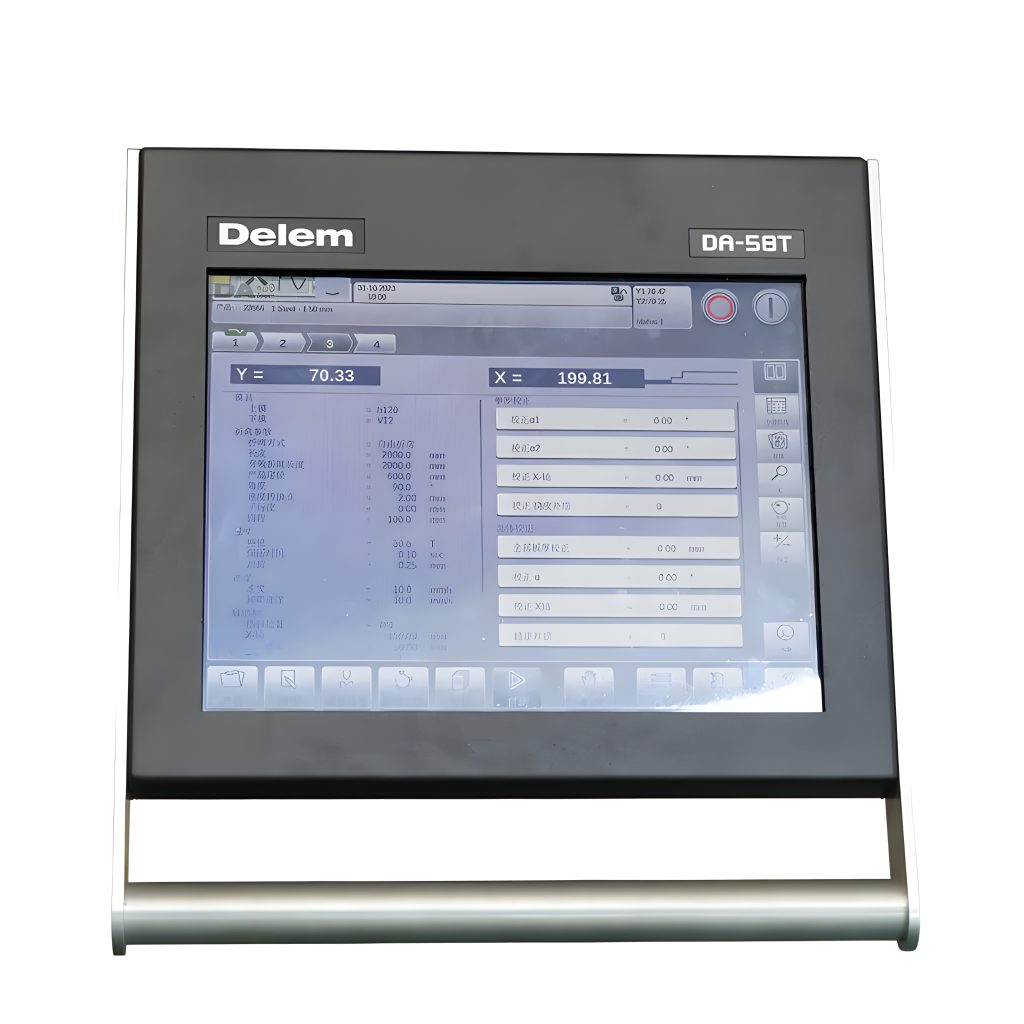
•2D touch graphics programming •15° high resolution TFT true color display •Bending process planning •Disturbance compensation control •Servo and inverter control modes •Advanced Y-axis control algorithm can control both closed-loop and open-loop. • USB port
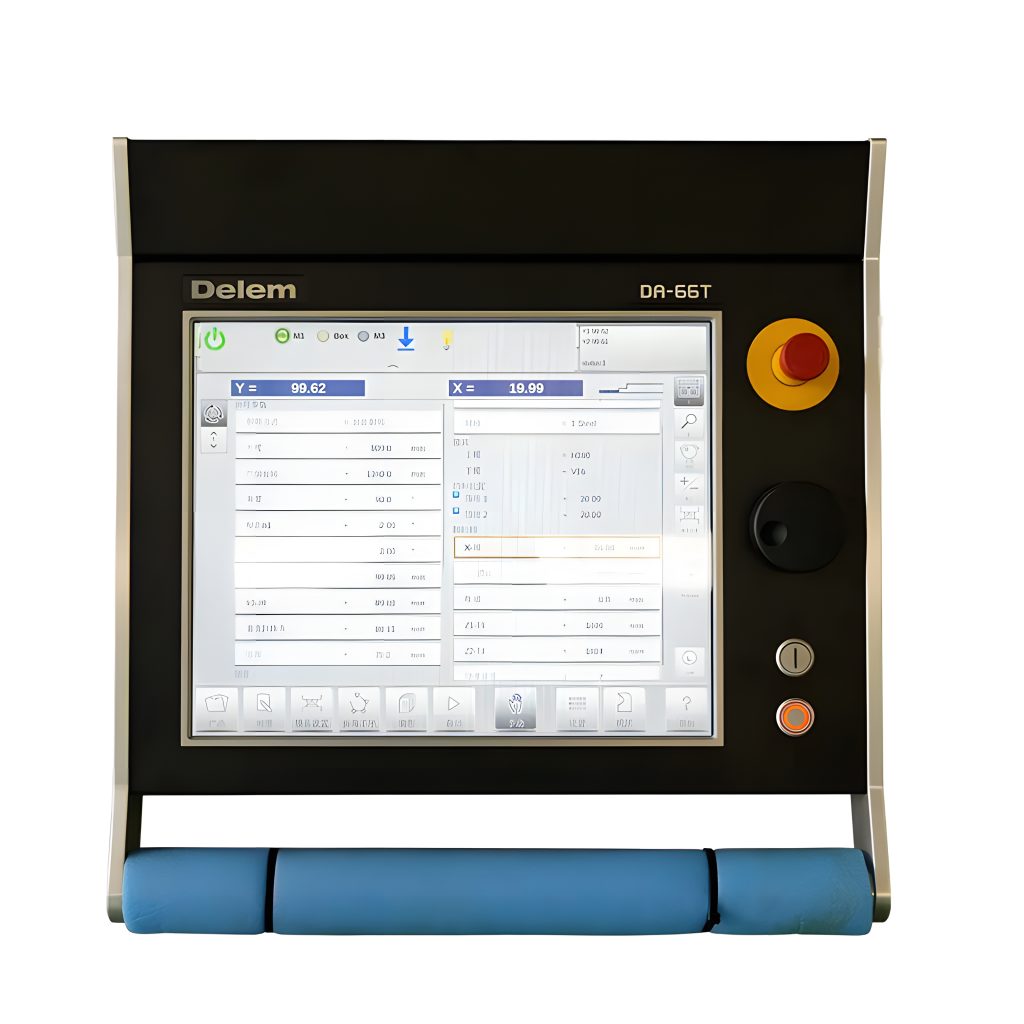
•2D touch graphics programming •3D product graphic simulation display •17" high resolution TFT true color display • COMPLETE WINDOWS APPLICATION PACKAGE •Compatible with DELEM modular structure system •USB, peripheral interface •User program application in multi-tasking environment •Angle detection sensor interface
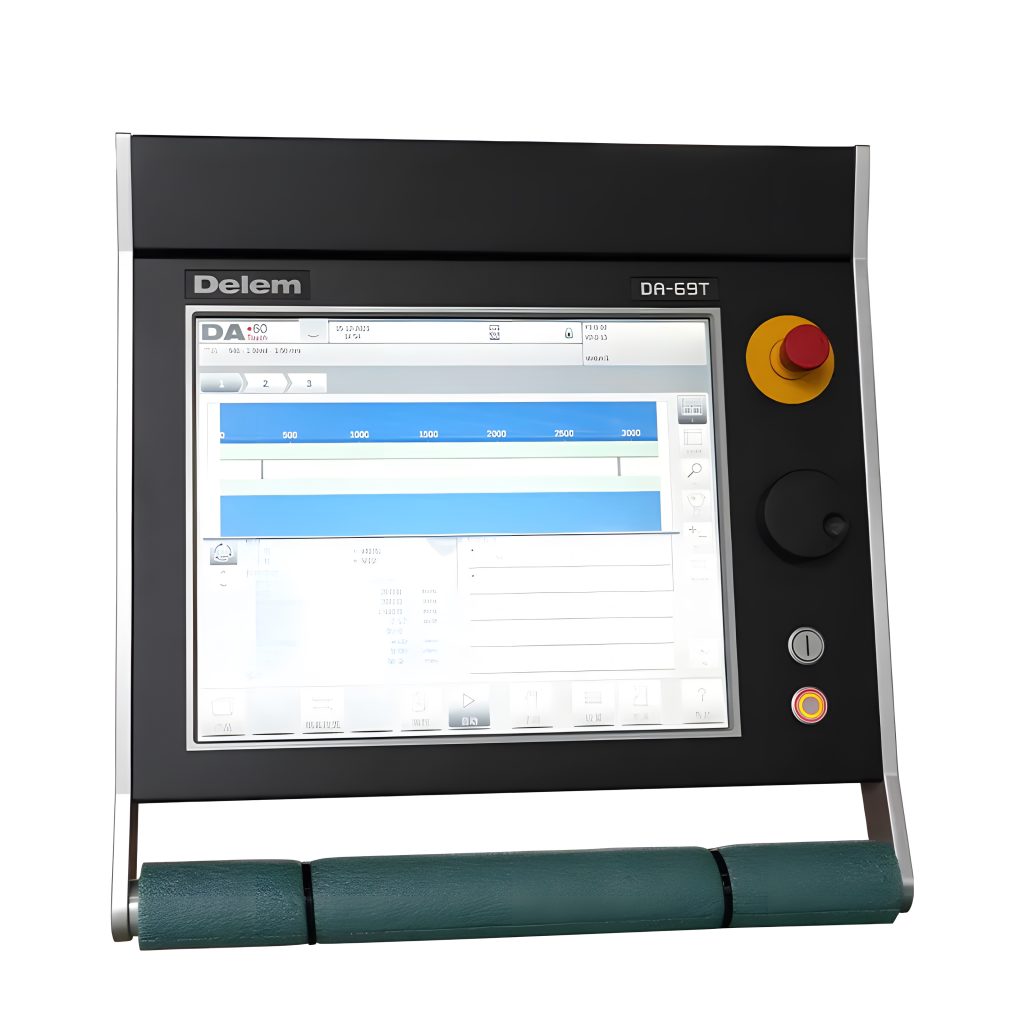
•2D and 3D touch graphics programming •30 product graphic simulation displays •17° high resolution TFT true color display •Compatible with DELEM modular structure system •USB, peripheral interface. •User program application in multi-tasking environment •Angle detection sensor interface
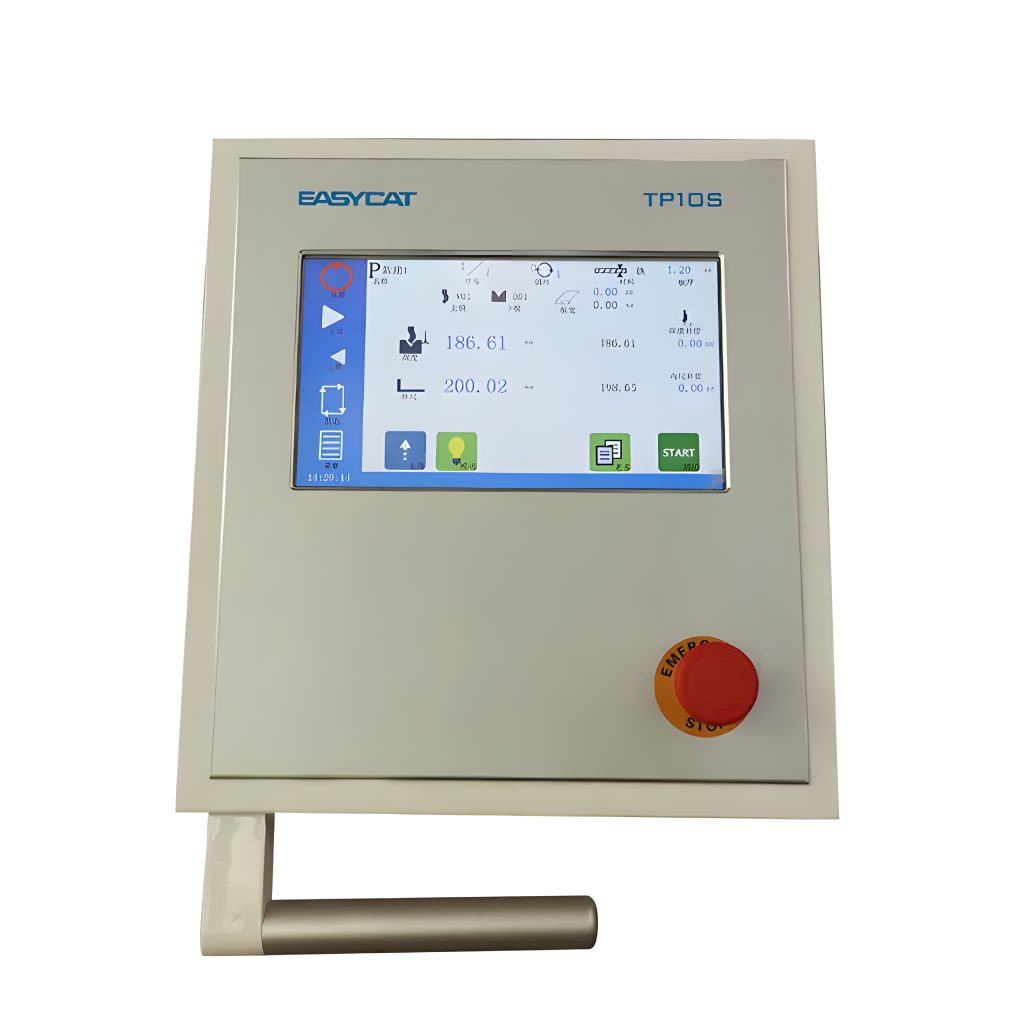
• Back gauge control • Control universal motors or inverters • Pressure holding and unloading time setting • Work piece count • Stores 40 programs with 25 steps each • Promotional features
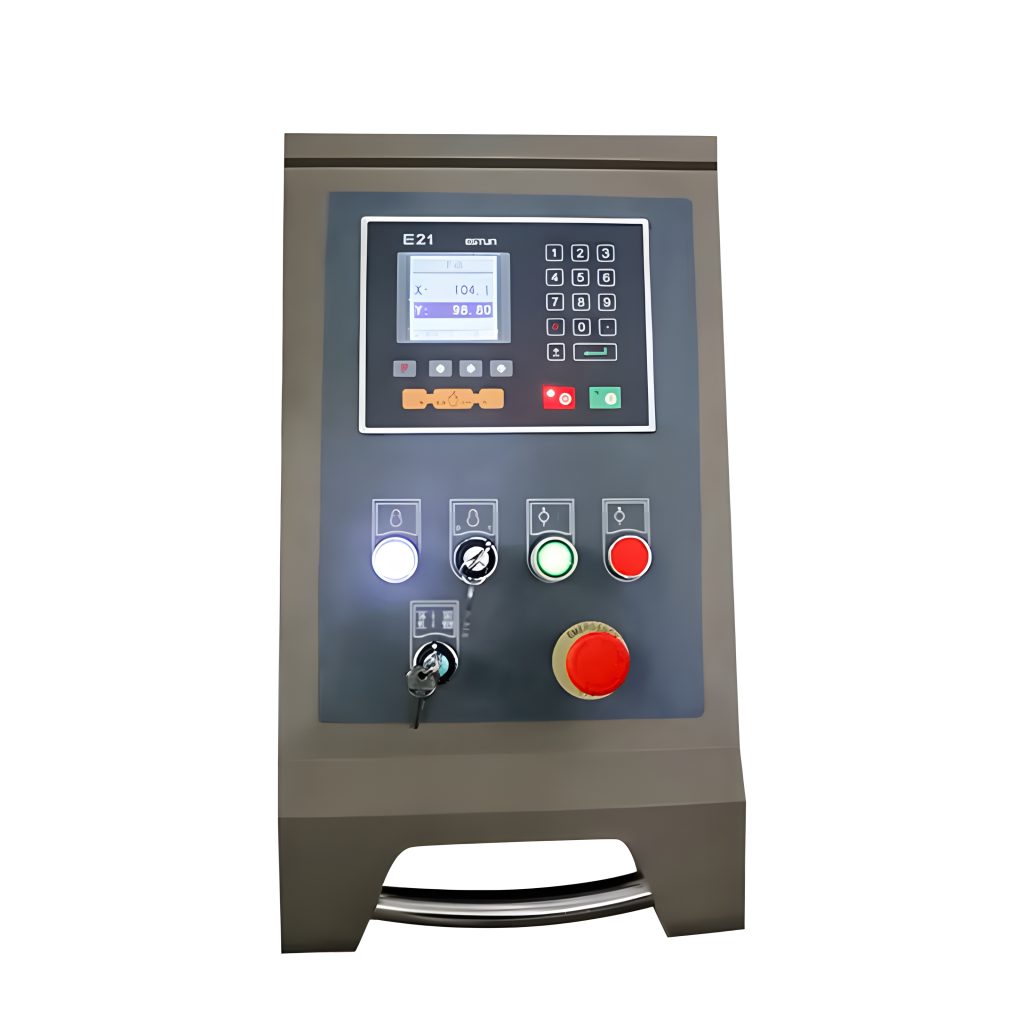
•Backgauge control •Control regular motors or inverters •Pressure holding and unloading time setting •Work piece count •Store 40 programs with 25 steps each •Preferential features
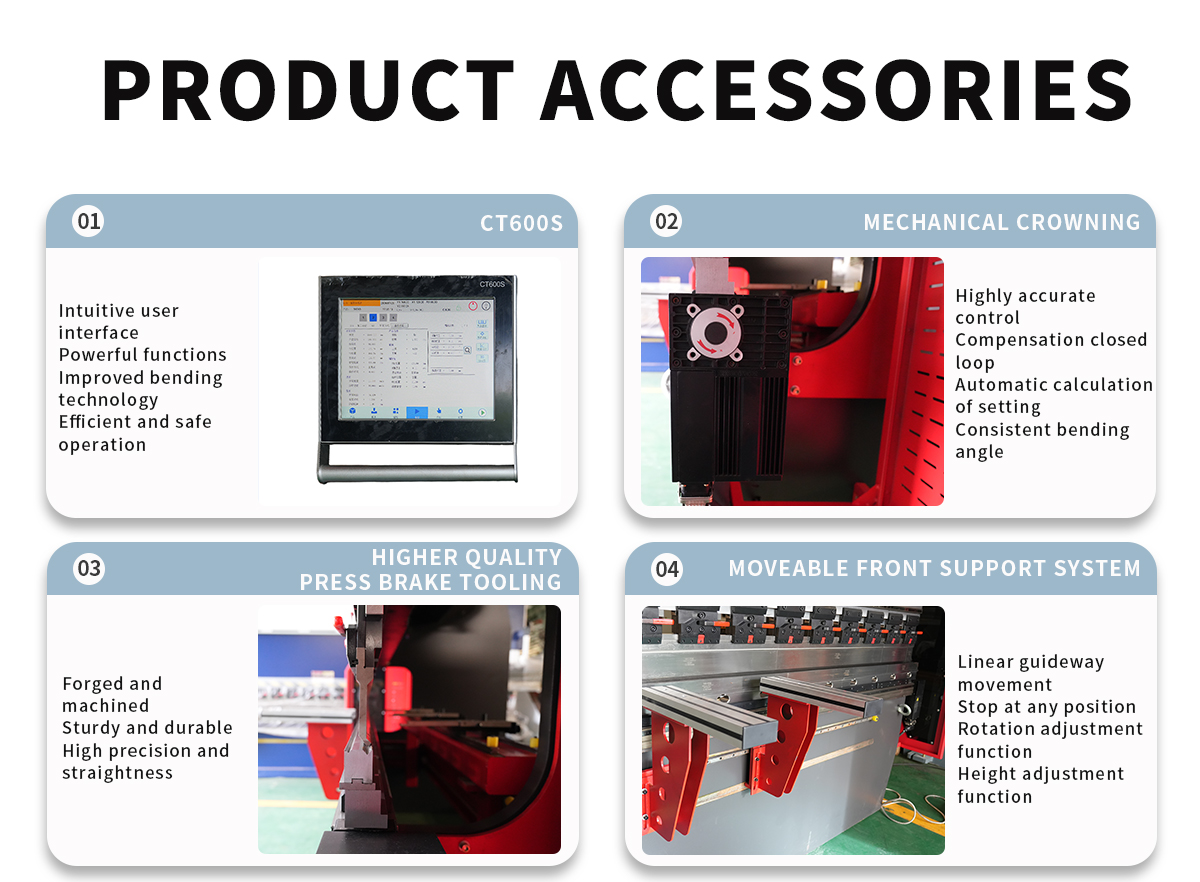
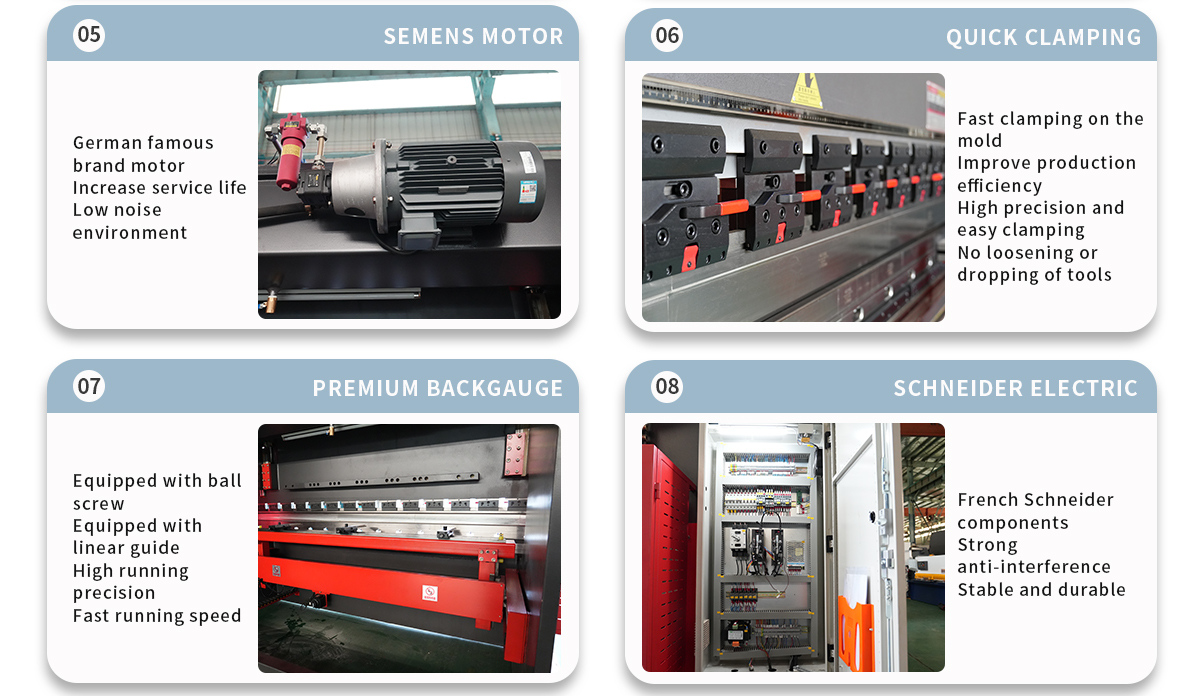
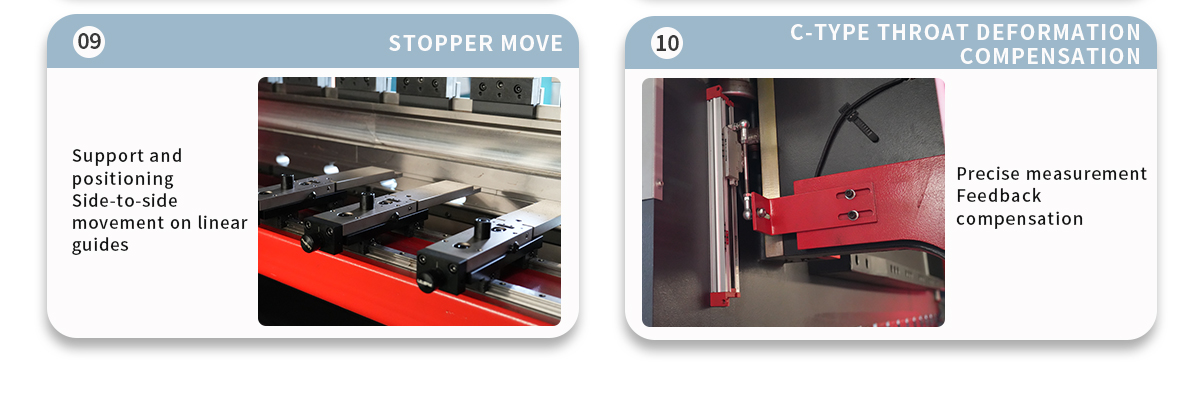

Type( WE67K series) | Nominal Force (KN) | Bending Length (mm) | Poles distance(mm) | Throat Depth(mm) | Slider Travel(mm) | Die Loading Height(mm) | Main Motor Power(kw) | Axes | Compensation cylinders |
63T/2500 | 630 | 2500 | 1900 | 350 | 170 | 380 | 5.5 | 4+1 | 2 |
80T/3200 | 800 | 3200 | 2700 | 350 | 170 | 380 | 7.5 | 4+1 | 3 |
100T/3200 | 100 | 3200 | 2700 | 400 | 200 | 420 | 7.5 | 4+1 | 3 |
160T/3200 | 1600 | 3200 | 2700 | 400 | 200 | 420 | 11 | 4+1 | 3 |
200T/3200 | 2000 | 3200 | 2700 | 400 | 200 | 420 | 15 | 4+1 | 3 |
250T/3200 | 2500 | 3200 | 2700 | 400 | 200 | 420 | 15 | 4+1 | 3 |
320T/3200 | 3200 | 3200 | 2700 | 400 | 200 | 420 | 22 | 4+1 | 3 |
400T/4000 | 4000 | 4000 | 3500 | 400 | 320 | 420 | 30 | 4+1 | Mechanical |
500T/5000 | 5000 | 5000 | 3900 | 500 | 320 | 600 | 37 | 4+1 | Mechanical |
600t/5000 | 6000 | 5000 | 3900 | 500 | 320 | 600 | 45 | 4+1 | Mechanical |
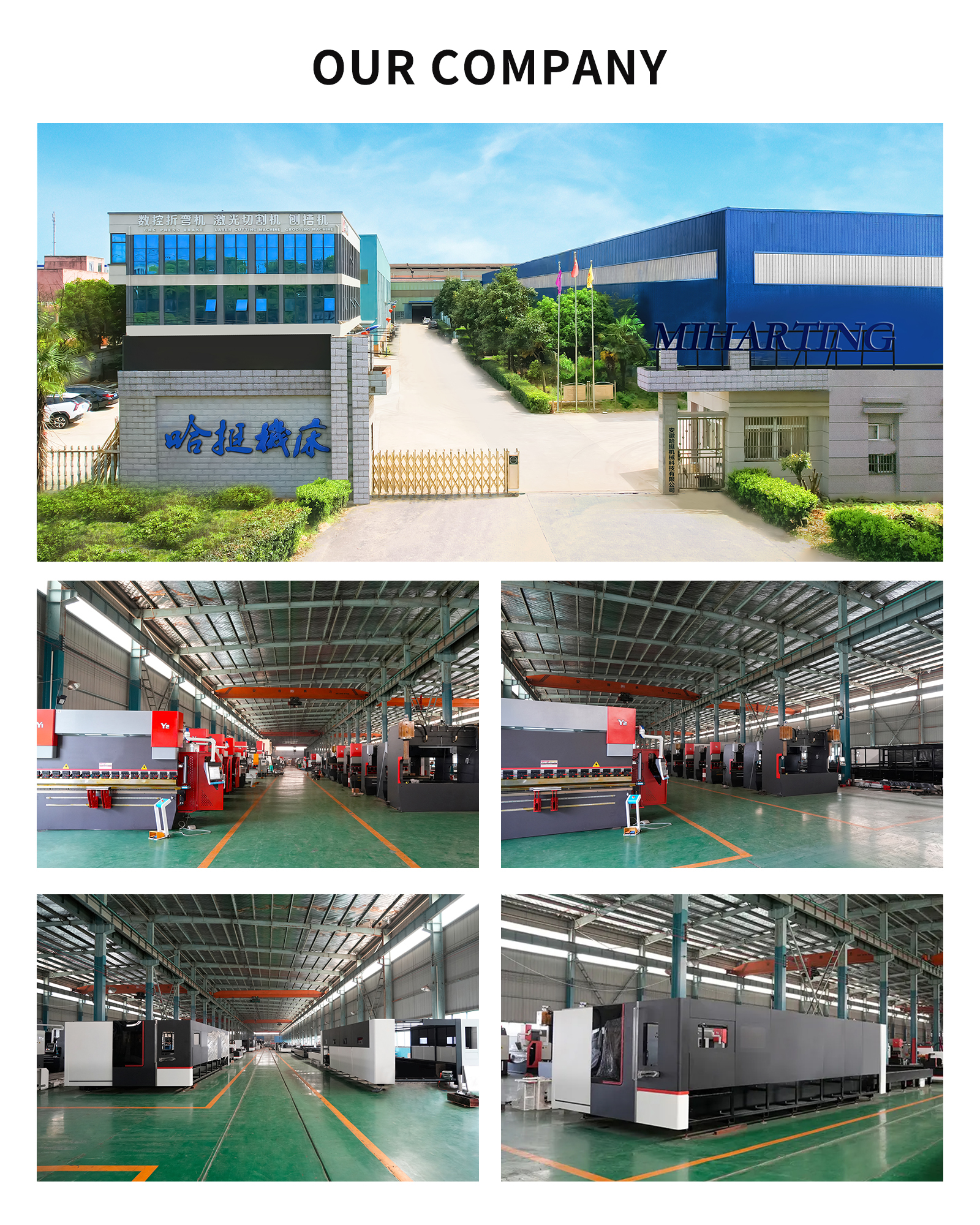
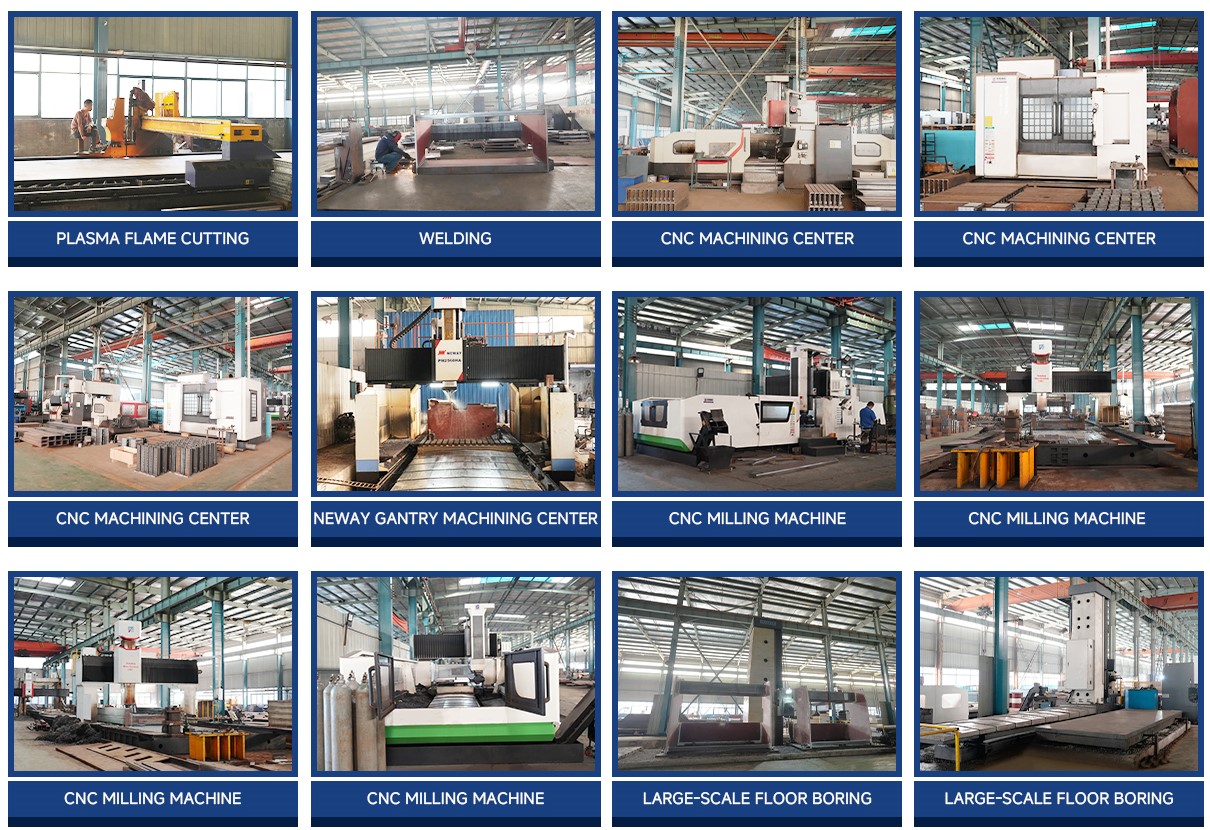
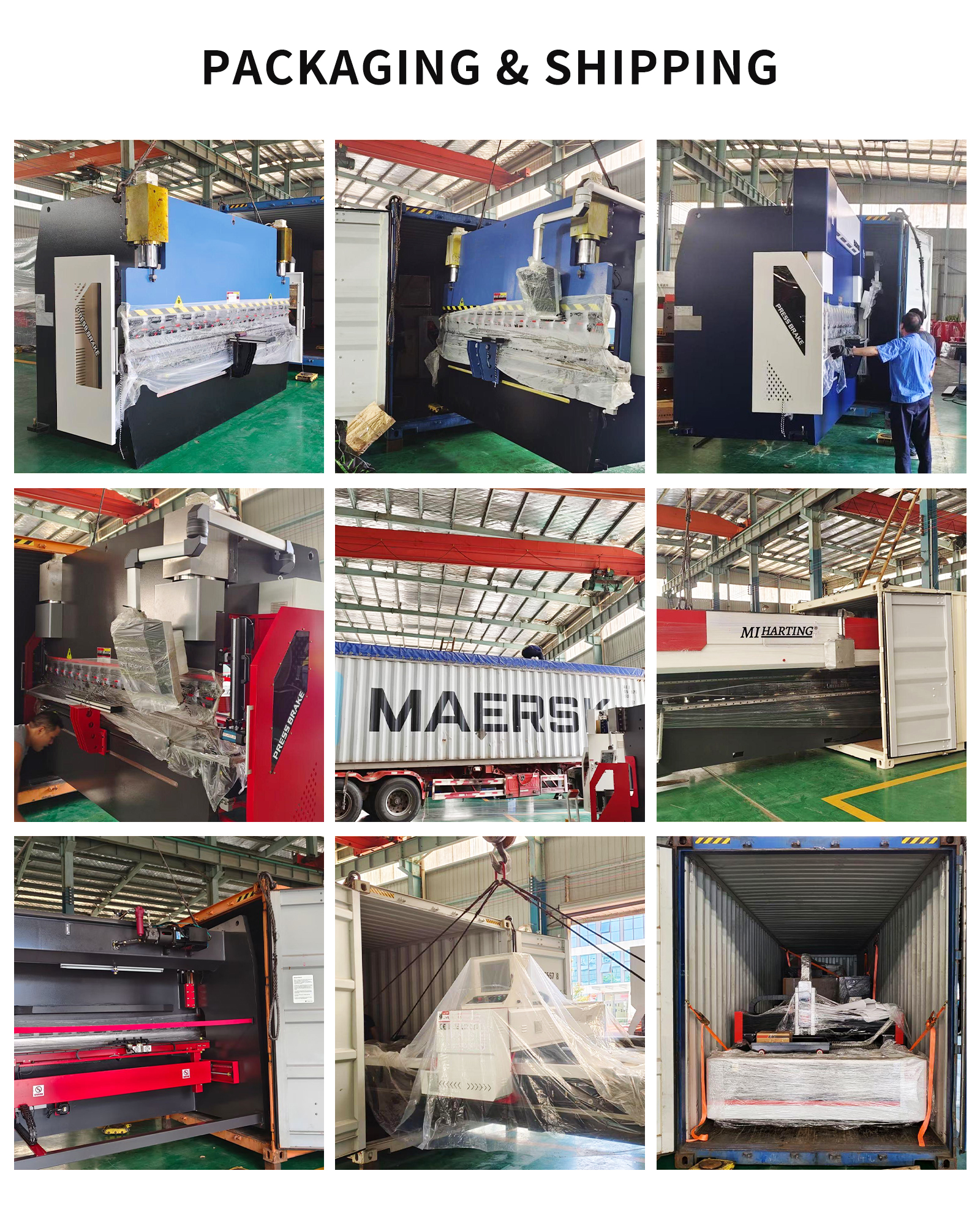