En el mundo de la fabricación de metales, varias máquinas clave desempeñan un papel vital en la conformación y el corte de metales con precisión y eficiencia. Esta guía definitiva brinda conocimientos e información integrales sobre los productos esenciales de la industria: plegadora, herramientas de plegadora, cizalla, máquina de corte por láser y prensa eléctrica. Ya sea que sea un principiante o un profesional experimentado, esta guía lo equipará con la información necesaria para comprender, seleccionar y optimizar el uso de estas máquinas para sus necesidades de trabajo con metales.
Presiona el freno:
1.¿Qué es una prensa plegadora?
Una prensa plegadora es un equipo clave que se utiliza en el campo de la fabricación de metales para doblar y plegar láminas de metal. Utiliza presión para doblar la hoja de metal en la forma deseada. Se usa comúnmente para crear piezas dobladas, recintos, tuberías y otros componentes metálicos.
Una prensa plegadora consta de un troquel superior y un troquel inferior, con el troquel superior fijado al marco y el troquel inferior móvil a través de un sistema hidráulico o un sistema de accionamiento mecánico. La hoja de metal se coloca entre los dos troqueles y luego se dobla en el ángulo y la forma deseados aplicando presión.
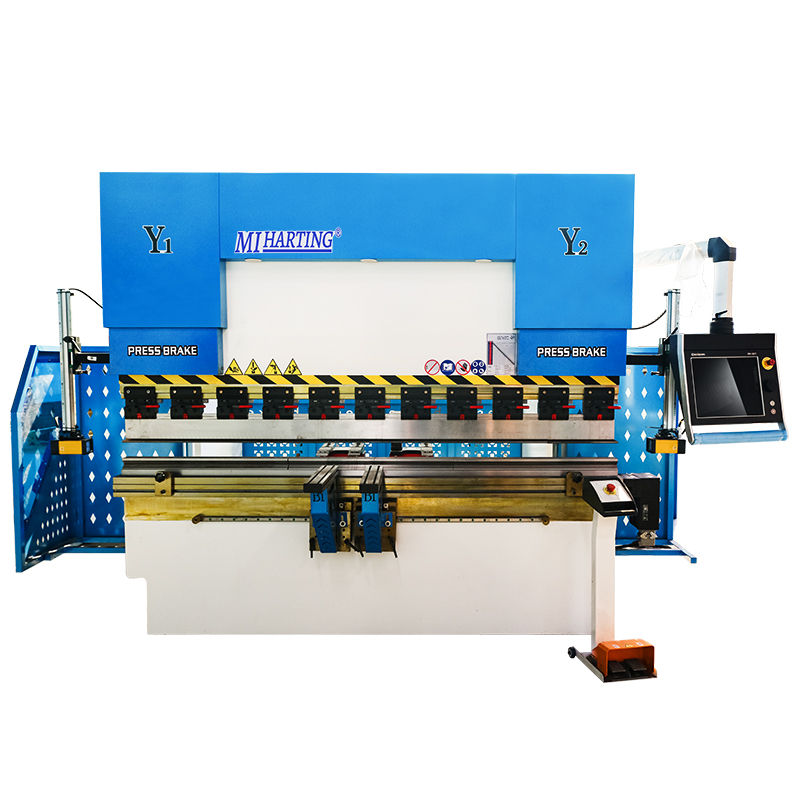
Las prensas plegadoras suelen tener las siguientes características y capacidades:
(1)Capacidad de plegado: las prensas plegadoras pueden lograr plegados en diferentes ángulos y radios para cumplir con los diversos requisitos de la pieza de trabajo.
(2) Precisión: se pueden lograr resultados de doblado de alta precisión ajustando la posición de los troqueles superior e inferior.
(3) Automatización: algunas prensas plegadoras modernas están equipadas con sistemas CNC, lo que permite una operación y programación automatizadas.
(4) Versatilidad: las prensas plegadoras se pueden usar para varias tareas de doblado y diferentes tipos de materiales metálicos cambiando diferentes herramientas y troqueles.
(5) Seguridad: las prensas plegadoras suelen estar equipadas con dispositivos de seguridad como cortinas de luz, cubiertas protectoras y botones de parada de emergencia para garantizar la seguridad del operador.
Las prensas plegadoras se utilizan ampliamente en industrias como la fabricación de automóviles, aeroespacial, construcción, electrónica y más. Son equipos esenciales para lograr una fabricación de metal precisa y eficiente.
Hay varios tipos de prensas plegadoras comúnmente utilizadas en la fabricación de metal:
Prensa plegadora mecánica: utiliza un volante mecánico y un sistema de embrague para doblar.
Prensa plegadora hidráulica: utiliza cilindros hidráulicos para un control de plegado preciso.
Prensa plegadora servoeléctrica: utiliza servomotores eléctricos para doblar con alta precisión.
Prensa plegadora neumática: se basa en aire comprimido para aplicaciones más ligeras.
Prensa plegadora CNC: Equipada con controles computarizados para operaciones de doblado automatizadas y precisas.
La elección de la plegadora depende de factores como el tipo de material, el grosor, los requisitos de doblado y el volumen de producción.
3. Componentes y principios de funcionamiento
Una prensa plegadora consta de varios componentes clave que trabajan juntos para realizar la operación de doblado. Estos son los componentes principales y sus funciones:
Bastidor: El bastidor proporciona soporte estructural y estabilidad a la prensa plegadora.
Cama: La cama es una superficie plana donde se coloca el material a doblar.
Ram: El carnero es la parte móvil de la prensa plegadora que aplica fuerza al material para doblarlo.
Matriz: La matriz es una herramienta que da forma al material proporcionando un ángulo de flexión específico.
Punzón: El punzón es otra herramienta que presiona contra el material, trabajando en conjunto con el troquel para doblarlo.
Tope trasero: El tope trasero es un dispositivo ajustable que posiciona el material con precisión para una flexión uniforme.
4.Características y ventajas clave
Colocación del Material: El operador coloca la lámina o placa de metal sobre la bancada de la prensa plegadora.
Configuración de la herramienta: Se seleccionan e instalan el troquel y el punzón apropiados en la prensa plegadora.
Ajuste del tope trasero: El tope trasero se ajusta para colocar el material correctamente para la curvatura deseada.
Proceso de doblado: el ariete se mueve hacia abajo, aplicando fuerza al material, que se intercala entre el punzón y la matriz. Esta acción de flexión crea el ángulo deseado en el material.
Eliminación de material: una vez que se completa el doblado, el operador elimina el material doblado de la prensa plegadora.
5.Aplicaciones e Industrias
Las prensas plegadoras se utilizan ampliamente en diversas industrias para diferentes aplicaciones, que incluyen:
Fabricación de metal: las prensas plegadoras se usan comúnmente en talleres de fabricación de metal para doblar y dar forma a láminas y placas de metal para diversos productos, como gabinetes, soportes, marcos y paneles.
Industria automotriz: las prensas plegadoras se utilizan en la industria automotriz para fabricar componentes como chasis, soportes y paneles de carrocería.
Industria aeroespacial: las prensas plegadoras se utilizan en la industria aeroespacial para doblar y formar piezas metálicas utilizadas en estructuras y componentes de aeronaves.
Construcción y Arquitectura: Las prensas plegadoras se utilizan en los sectores de la construcción y la arquitectura para doblar componentes metálicos utilizados en estructuras de edificios, fachadas y elementos decorativos.
Electrónica y electrodomésticos: las prensas plegadoras se emplean en la fabricación de gabinetes electrónicos, componentes de electrodomésticos y productos de consumo.
Herramientas de freno de prensa:
1. Importancia de las herramientas de plegadora
Las herramientas de prensa plegadora juegan un papel crucial en el rendimiento y la eficiencia de las máquinas plegadoras. Estos son algunos puntos clave que destacan la importancia de las herramientas de plegadora:
(1) Doblado de precisión: las herramientas de plegadoras están diseñadas para proporcionar ángulos de doblado precisos y precisos. Aseguran resultados consistentes y ayudan a cumplir con las especificaciones requeridas para el producto final. La calidad y precisión de las herramientas impactan directamente en la calidad general de las piezas dobladas.
(2) Versatilidad: las herramientas de plegadoras vienen en varias formas, tamaños y configuraciones para adaptarse a diferentes requisitos de doblado. Se pueden personalizar o intercambiar para lograr diferentes ángulos de plegado, radios o formas complejas. Esta versatilidad permite a los fabricantes producir una amplia gama de productos utilizando la misma máquina.
(3) Durabilidad y longevidad: las herramientas de plegadoras están fabricadas con materiales de alta calidad, como acero endurecido o aleaciones especiales, lo que las hace muy duraderas y resistentes al desgaste. El mantenimiento adecuado y las inspecciones periódicas de las herramientas garantizan su longevidad, lo que reduce la necesidad de reemplazos frecuentes.
(4) Eficiencia y productividad: las herramientas de plegadoras bien diseñadas optimizan el proceso de doblado, reducen el tiempo de preparación y aumentan la productividad. Permiten ciclos de plegado más rápidos, lo que permite a los fabricantes producir más piezas en menos tiempo. Las herramientas eficientes también minimizan el desperdicio de material y mejoran la eficiencia general de la producción.
(5) Ahorro de costos: el uso de las herramientas de plegadora correctas puede generar ahorros de costos de varias maneras. El doblado preciso reduce el desperdicio de material, ahorrando costos de materia prima. Las herramientas eficientes reducen el tiempo de configuración y aumentan la productividad de la máquina, maximizando la producción por hora. Además, las herramientas duraderas tienen una vida útil más larga, lo que reduce la frecuencia de los reemplazos y los costos de mantenimiento.
(6) Seguridad: Las herramientas de prensa plegadora están diseñadas teniendo en cuenta las características de seguridad. Proporcionan mecanismos de sujeción y sujeción adecuados para asegurar el material durante el plegado, minimizando el riesgo de accidentes. Además, el uso de herramientas de alta calidad reduce las posibilidades de falla o rotura de la herramienta, lo que garantiza la seguridad del operador.
(7) En resumen, las herramientas de plegadora son vitales para lograr resultados de plegado precisos y precisos, mejorar la productividad, reducir costos y garantizar la seguridad del operador. Seleccionar las herramientas correctas y mantenerlas adecuadamente es esencial para la operación eficiente de las máquinas plegadoras.
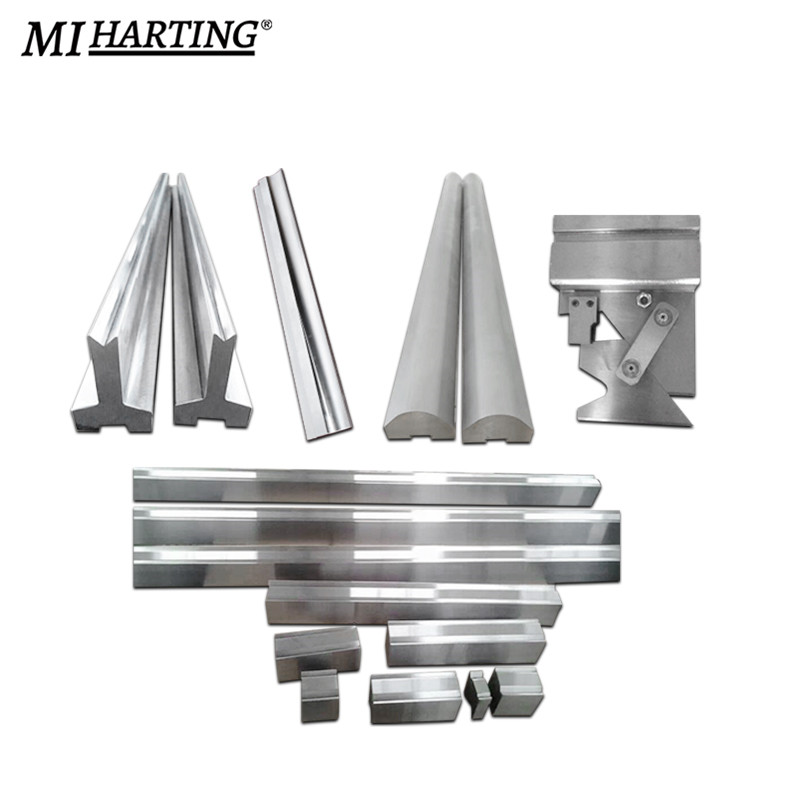
2. Tipos de herramientas de freno de prensa (incluidas las herramientas de freno de prensa ARC)
Hay varios tipos de herramientas de plegadora disponibles, cada una diseñada para aplicaciones específicas de doblado. Estos son algunos tipos comunes de herramientas de plegadora:
Troquel en V: Los troqueles en V son las herramientas de plegadora más utilizadas. Consisten en un troquel inferior con una ranura en forma de V y un punzón con una punta en forma de V a juego. Los troqueles en V son versátiles y se pueden utilizar para una amplia gama de ángulos de doblado y materiales.
(1) Troquel de fondo: Los troqueles de fondo, también conocidos como troqueles planos, tienen una superficie plana en lugar de una ranura en forma de V. Se utilizan para lograr curvas pronunciadas o doblar materiales más gruesos donde se requiere un radio más estrecho.
(2) Punzón de cuello de cisne: Los punzones de cuello de cisne tienen una forma curva que permite dobleces profundos y compensados. Se utilizan comúnmente para doblar canales, cajas y otras formas complejas.
(3) Herramienta de dobladillo: las herramientas de dobladillo se utilizan para crear dobladillos o pestañas en el borde de una pieza de chapa metálica. Consisten en un juego de punzón y troquel que dobla el material sobre sí mismo para crear un borde seguro.
(4) Herramienta de radio: las herramientas de radio, también conocidas como punzones de radio o matrices de radio, se utilizan para crear pliegues curvos con un radio específico. Están disponibles en varios tamaños para adaptarse a diferentes requisitos de flexión.
(5) Troquel Multi-V: Los troqueles Multi-V tienen múltiples ranuras en forma de V de diferentes tamaños en un solo troquel. Permiten cambios de herramienta rápidos y sencillos sin necesidad de troqueles separados para diferentes ángulos de doblado.
(6) Herramientas de plegadora ARC: Las herramientas de plegadora ARC son herramientas especializadas que se utilizan para doblar láminas de metal en forma de arco. Están diseñados para crear curvas curvas precisas y consistentes, comúnmente utilizadas en aplicaciones como piezas cilíndricas, tubos o perfiles curvos.
Las herramientas de plegadora ARC generalmente consisten en un troquel inferior con una ranura curva y un punzón con una punta curva a juego. Permiten el doblado preciso y repetible de láminas de metal en varias formas de arco.
3. Selección de materiales y recubrimientos
Cuando se trata de herramientas para plegadoras, la selección de materiales y los recubrimientos juegan un papel importante en su rendimiento y longevidad. Aquí hay una breve descripción general de la selección de materiales y recubrimientos para herramientas de plegadora:
Selección de materiales:
(1) Acero para herramientas: El acero para herramientas, como D2 o A2, se usa comúnmente para herramientas de plegadoras debido a su alta dureza, resistencia al desgaste y tenacidad.
(2) Carburo: Los insertos o puntas de carburo se usan para aplicaciones de servicio pesado o cuando se doblan materiales abrasivos. El carburo proporciona una excelente resistencia al desgaste, pero es más frágil que el acero para herramientas.
(3) Acero de alta velocidad (HSS): HSS es otra opción para herramientas de plegadora. Ofrece buena tenacidad y resistencia al desgaste, pero no tan alta como el acero para herramientas.
Recubrimientos:
(4) Recubrimiento de nitruro: Los recubrimientos de nitruro, como TiN (nitruro de titanio) o TiCN (carbonitruro de titanio), mejoran la dureza de la superficie y la resistencia al desgaste de la herramienta. Son adecuados para aplicaciones de plegado de propósito general.
(5) Recubrimiento DLC: Los recubrimientos DLC (carbono similar al diamante) brindan una excelente dureza, baja fricción y alta resistencia al desgaste. Son ideales para doblar acero inoxidable y otros materiales difíciles de moldear.
(6) Recubrimiento PVD: Los recubrimientos de deposición física de vapor (PVD), como TiAlN (nitruro de titanio y aluminio), mejoran el rendimiento de la herramienta al reducir la fricción y aumentar la resistencia al desgaste.
(7) Revestimiento de cromo: El revestimiento de cromo es un revestimiento común para las herramientas de plegadora. Proporciona buena resistencia a la corrosión y reduce la fricción durante las operaciones de doblado.
La selección del material y el revestimiento depende de factores como el tipo de material que se dobla, la aplicación de doblado y la vida útil deseada de la herramienta. Es importante elegir la combinación correcta de material y revestimiento para garantizar un rendimiento y una durabilidad óptimos de las herramientas de la prensa plegadora.
4. Configuraciones y consideraciones de herramientas
Cuando se trata de herramientas de plegadora, las configuraciones y consideraciones de las herramientas son cruciales para lograr operaciones de plegado precisas y eficientes. Aquí hay algunos aspectos importantes a considerar:
Configuraciones de herramientas:
(1) Troquel en V: El troquel en V es la herramienta hembra que proporciona la forma de curvatura deseada. Viene en varios anchos y ángulos para adaptarse a diferentes espesores de material y requisitos de flexión.
(2) Punzón: El punzón es la herramienta macho que hace contacto con el material y aplica fuerza para crear el doblez. También viene en diferentes formas y tamaños para lograr radios y ángulos de curvatura específicos.
(3) Troquel Multi-V: Los troqueles Multi-V tienen múltiples ranuras en forma de V de diferentes anchos y ángulos. Permiten doblar diferentes espesores y ángulos de material sin cambiar el troquel.
(4) Punzón de cuello de cisne: los punzones de cuello de cisne tienen una forma curva que permite dobleces profundos o desplazados donde el espacio es limitado.
(5) Herramientas de dobladillo: las herramientas de dobladillo se utilizan para crear bordes doblados o pestañas en láminas de metal.
Consideraciones:
(1) Grosor del material: la configuración de herramientas debe seleccionarse en función del grosor del material que se dobla. Los materiales más gruesos pueden requerir herramientas más grandes para adaptarse a la mayor fuerza y evitar daños a la herramienta.
(2) Tipo de material: diferentes materiales tienen propiedades variables, como dureza y ductilidad, que pueden afectar la selección de herramientas. Los materiales más duros pueden requerir materiales o recubrimientos de herramientas más duros.
(3) Ángulo de curvatura y radio: El ángulo de curvatura y el radio deseados dictan la selección de configuraciones de punzón y matriz. Las curvas pronunciadas requieren radios de perforación más pequeños, mientras que se necesitan radios más grandes para curvas más suaves.
(4) Alineación de herramientas: la alineación adecuada entre el punzón y la matriz es esencial para lograr dobleces precisos y consistentes. La desalineación puede provocar dobleces irregulares o daños en la herramienta.
(5) Mantenimiento de herramientas: la inspección y el mantenimiento regulares de las herramientas son necesarios para garantizar un rendimiento y una longevidad óptimos. Esto incluye limpieza, lubricación y reemplazo de componentes desgastados.
Al considerar las configuraciones de herramientas y estos factores importantes, puede seleccionar las herramientas de plegadora apropiadas para sus requisitos de doblado específicos. Esto lo ayudará a lograr operaciones de doblado precisas y eficientes mientras prolonga la vida útil de las herramientas.
5. Mantenimiento y longevidad de la herramienta
(1) Limpieza regular: limpie las herramientas de la prensa plegadora con regularidad para eliminar los desechos, la suciedad y las virutas de metal. Utilice agentes de limpieza y herramientas apropiados para evitar dañar las superficies de las herramientas. Asegúrese de que las herramientas estén completamente secas antes de guardarlas.
(2) Lubricación: Aplique lubricación a las herramientas de la prensa dobladora según lo recomendado por el fabricante. La lubricación ayuda a reducir la fricción y el desgaste, mejorando la vida útil de la herramienta. Siga las pautas del fabricante para el tipo y la frecuencia de lubricación.
(3) Inspección y reparación: Inspeccione regularmente las herramientas de la prensa plegadora en busca de signos de desgaste, daño o deformación. Compruebe si hay grietas, astillas o desgaste excesivo en los bordes cortantes. Si se detecta algún problema, repare o reemplace de inmediato las piezas dañadas para evitar daños mayores y garantizar resultados de doblado precisos.
(4) Almacenamiento adecuado: almacene las herramientas de la prensa plegadora en un ambiente limpio y seco para evitar la corrosión y los daños. Use bastidores o cajas de herramientas especiales para mantener las herramientas organizadas y protegidas. Evite colocar objetos pesados encima de las herramientas para evitar que se deformen.
(5) Capacitación del operador: la capacitación adecuada de los operadores es esencial para el mantenimiento y la longevidad de la herramienta. Educar a los operadores sobre las técnicas de uso correctas, los límites operativos y las precauciones de seguridad. Anime a los operadores a informar cualquier problema o anormalidad con las herramientas de inmediato.
Siguiendo estos consejos de mantenimiento, puede prolongar la vida útil de sus herramientas de plegadora y garantizar operaciones de plegado consistentes y precisas. El mantenimiento regular no solo mejora el rendimiento de la herramienta, sino que también contribuye a la seguridad y eficiencia generales del proceso de plegado.
6. Tecnologías e innovaciones de herramientas avanzadas
Las tecnologías e innovaciones de herramientas avanzadas han mejorado significativamente el rendimiento y las capacidades de las herramientas de plegadora. Estos son algunos avances clave en el herramental para prensas plegadoras:
(1) Materiales de alta resistencia: el herramental de la plegadora ahora está hecho de materiales de alta resistencia, como aleaciones de acero endurecido o carburo. Estos materiales ofrecen una durabilidad superior, resistencia al desgaste y una mayor vida útil de la herramienta en comparación con los materiales de herramientas tradicionales.
(2) Recubrimientos y tratamientos superficiales: Se aplican recubrimientos y tratamientos superficiales avanzados, como TiN (nitruro de titanio) o DLC (carbono similar al diamante), a las herramientas de plegadora para mejorar su rendimiento. Estos recubrimientos reducen la fricción, mejoran la resistencia al desgaste y previenen la adhesión del material, lo que da como resultado una mejor calidad de doblado y una vida útil más larga de la herramienta.
(3) Sistemas de herramientas de precisión: Los modernos sistemas de herramientas para plegadoras cuentan con herramientas rectificadas con precisión con tolerancias estrechas. Estos sistemas aseguran resultados de plegado precisos y repetibles, reduciendo los tiempos de configuración y aumentando la productividad.
(4) Sistemas de herramientas de cambio rápido: los sistemas de herramientas de cambio rápido permiten una configuración y cambios de herramientas rápidos. Estos sistemas utilizan soportes de herramientas y mecanismos de sujeción estandarizados, lo que permite a los operadores cambiar entre diferentes configuraciones de herramientas de forma rápida y eficiente.
(5) Modelado y simulación en 3D: las herramientas de software avanzadas permiten el modelado y la simulación en 3D de los procesos de plegado. Estas herramientas ayudan a optimizar los diseños de herramientas, simular secuencias de doblado y detectar posibles problemas de colisión o interferencia antes de la producción real. Esto reduce el tiempo de configuración, minimiza los errores y mejora la eficiencia general.
(6) Soluciones de herramientas personalizadas: los fabricantes de herramientas ahora ofrecen soluciones de herramientas personalizadas adaptadas a aplicaciones de doblado específicas. Estas soluciones incluyen perfiles de herramientas especializados, recubrimientos de herramientas personalizados e incluso herramientas con sensores integrados para el monitoreo y control de procesos.
Estos avances en las tecnologías de herramientas para plegadoras han mejorado significativamente la productividad, la precisión y la vida útil de la herramienta. Al adoptar estas innovaciones, los fabricantes pueden lograr una mayor eficiencia, reducir el tiempo de inactividad y producir piezas dobladas de alta calidad de manera constante.
1. Comprender las máquinas de corte
Las cizallas son dispositivos mecánicos industriales que se utilizan para cortar láminas de metal y otros materiales. Aplican fuerza de corte para cortar los materiales en las formas y tamaños deseados. Las cizallas se utilizan ampliamente en las industrias de fabricación y metalurgia para producir diversos productos y componentes.
El principio de funcionamiento de las cizallas consiste en colocar el material sobre una mesa de cizalla y aplicar fuerza a través de cuchillas de corte para que el material se rompa. Las cizallas pueden realizar operaciones como corte recto, corte curvo y corte en ángulo. Dependiendo de los requisitos específicos, las cizallas pueden tener diferentes capacidades de corte y precisión.
Hay varios tipos de cizallas, incluidas cizallas hidráulicas, cizallas mecánicas y cizallas manuales. Las cizallas hidráulicas utilizan sistemas hidráulicos para proporcionar fuerza de corte y ofrecen alta potencia y precisión, lo que las hace adecuadas para tareas de corte de gran escala y trabajo pesado. Las cizallas mecánicas utilizan mecanismos mecánicos para proporcionar fuerza de corte y, por lo general, son más compactas y rentables, adecuadas para tareas de corte de tamaño mediano. Las cizallas manuales requieren operación manual y son adecuadas para trabajos de corte simples y de pequeña escala.
La capacidad de corte de las cizallas depende de su espesor máximo de corte y ancho de corte. Las cizallas más grandes generalmente tienen una mayor capacidad de corte y pueden manejar materiales más gruesos y anchos. La precisión de corte de las cizallas está influenciada por factores como el filo de la cuchilla, el ajuste de la holgura de la cuchilla, la rigidez del marco y las características del material.
Las consideraciones de seguridad son importantes al operar máquinas cortadoras. Los operadores deben recibir una formación adecuada sobre los procedimientos de funcionamiento y las precauciones de seguridad de las cizallas. Además, se debe usar el equipo de protección personal adecuado, como gafas de seguridad y guantes. La inspección y el mantenimiento regulares de las cizallas son necesarios para garantizar su correcto funcionamiento y operación segura. Seguir el manual de operación y las recomendaciones del fabricante es fundamental para garantizar la seguridad y la eficacia de la operación de las cizallas.
En resumen, las cizallas son herramientas de corte esenciales ampliamente utilizadas en las industrias manufacturera y metalúrgica. Comprender los principios, los tipos, la capacidad de corte y las precauciones de seguridad de las cizallas puede ayudar a seleccionar la máquina adecuada y operarla de manera segura y eficiente.
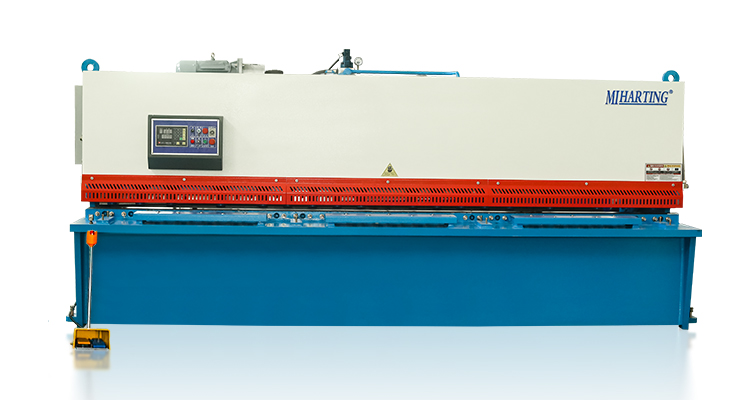
2. Cizallas hidráulicas vs. mecánicas
Las cizallas hidráulicas y mecánicas son dos tipos comunes de cizallas utilizadas en aplicaciones industriales. Aquí hay una comparación entre los dos:
Fuente de alimentación:
(1) Cizallas hidráulicas: estas máquinas utilizan un sistema hidráulico para generar la fuerza de corte. La fuerza se aplica a través de cilindros hidráulicos accionados por una bomba hidráulica. Las cizallas hidráulicas ofrecen alta potencia y pueden manejar operaciones de corte de trabajo pesado.
(2) Cizallas mecánicas: estas máquinas utilizan mecanismos mecánicos, como engranajes, palancas y volantes, para generar la fuerza de corte. La fuerza se aplica directamente a través de los componentes mecánicos. Las cizallas mecánicas son generalmente más compactas y rentables.
Potencia y Precisión:
(1) Máquinas cizallas hidráulicas: debido al sistema hidráulico, las máquinas cizallas hidráulicas pueden proporcionar una gran potencia de corte. Son capaces de cortar materiales gruesos y duros con precisión. El sistema hidráulico permite un mejor control y ajuste de la fuerza de corte, lo que da como resultado cortes precisos y uniformes.
(2) Cizallas mecánicas: Las cizallas mecánicas proporcionan una potencia de corte menor en comparación con las hidráulicas. Son adecuados para tareas de corte de servicio medio. Sin embargo, la precisión de corte de las cizallas mecánicas puede verse afectada por factores como el desgaste mecánico, que pueden requerir ajustes y mantenimiento más frecuentes.
Tamaño y espacio:
(3) Máquinas cizallas hidráulicas: Las máquinas cizallas hidráulicas son generalmente más grandes y requieren más espacio debido a los componentes del sistema hidráulico, como la bomba hidráulica, los cilindros y las mangueras.
(4) Cizallas mecánicas: las cizallas mecánicas son más compactas y ocupan menos espacio. A menudo se prefieren en talleres más pequeños o donde el espacio es limitado.
Costo:
(1) Cizallas hidráulicas: Las cizallas hidráulicas suelen ser más caras debido a la complejidad y el costo de los componentes del sistema hidráulico.
(2) Cizallas mecánicas: Las cizallas mecánicas son generalmente más asequibles y rentables.
En resumen, las cizallas hidráulicas brindan alta potencia y precisión, lo que las hace adecuadas para operaciones de corte de trabajo pesado. Son más grandes y más caros. Por otro lado, las cizallas mecánicas son más compactas, rentables y adecuadas para tareas de corte medianas. La elección entre cizallas hidráulicas y mecánicas depende de los requisitos de corte específicos, el espacio disponible y las consideraciones presupuestarias.
3. Componentes y Operación
Componentes de una cizalla:
(1) Mesa de corte: esta es la superficie plana o cama sobre la cual se coloca el material a cortar. Proporciona soporte y estabilidad durante el proceso de corte.
(2) Cuchillas de corte: estas son las cuchillas afiladas que realizan el corte real del material. Por lo general, están hechos de acero para herramientas de alta calidad y están montados de forma segura en la máquina. Las cuchillas pueden ser rectas, curvas o en ángulo, según la operación de corte deseada.
(3) Ajuste de la holgura de las cuchillas: Las cizallas suelen tener un mecanismo para ajustar la holgura entre las cuchillas superior e inferior. Este ajuste permite un control preciso del espacio de corte, asegurando cortes limpios y precisos.
(4) Tope trasero: El tope trasero es un tope móvil o una guía ubicada detrás de la mesa de corte. Ayuda a colocar el material con precisión para operaciones de corte repetitivas. El tope trasero puede ajustarse manualmente o controlarse mediante un sistema motorizado.
(5) Sistema de accionamiento: El sistema de accionamiento proporciona la potencia para mover las cuchillas de corte. En las cizallas hidráulicas, el sistema de accionamiento consta de una bomba hidráulica, cilindros y válvulas. En las cizallas mecánicas, normalmente involucra componentes mecánicos como engranajes, palancas y volantes.
(6) Panel de control: El panel de control alberga los controles e interruptores para operar la máquina cortadora. Le permite al operador iniciar y detener la máquina, ajustar la configuración y monitorear el proceso de corte.
Operación de una máquina cortadora:
(1) Preparación del material: el material que se va a cortar se prepara asegurándose de que esté limpio, recto y correctamente alineado con la mesa de corte. Deben eliminarse todos los revestimientos o películas protectoras del material.
(2) Colocación del material: el material se coloca en la mesa de corte, asegurándose de que esté alineado con el tope trasero, si corresponde. El operador debe tener cuidado de colocar el material de forma segura y evitar obstrucciones que puedan interferir con el proceso de corte.
(3) Ajuste de la holgura de la hoja: la holgura de la hoja se ajusta de acuerdo con el grosor y el tipo de material que se corta. Este ajuste asegura un cizallamiento adecuado sin dañar el material ni las cuchillas. Se deben seguir las pautas del fabricante o el manual de la máquina para la configuración correcta de la holgura de la hoja.
(4) Operación de corte: Una vez que el material se coloca correctamente y se establece la holgura de la cuchilla, el operador inicia la operación de corte. En las cizallas hidráulicas, la bomba hidráulica se activa para proporcionar la fuerza de corte necesaria. En las cizallas mecánicas, el operador activa el sistema de accionamiento, que transfiere potencia a las cuchillas de corte.
(5) Supervisión y control: durante el proceso de corte, el operador supervisa la operación para garantizar un corte suave y preciso. El panel de control puede proporcionar indicadores o pantallas para monitorear la velocidad de corte, la posición de la cuchilla y otros parámetros. Cualquier anomalía o problema debe abordarse de inmediato.
(6) Eliminación de material y repetición: una vez completada la operación de corte, las piezas cortadas se retiran de la mesa de corte. El proceso se puede repetir para cortes posteriores, ajustando el tope trasero si es necesario.
Es importante tener en cuenta que el funcionamiento específico de una cizalla puede variar según el modelo y el fabricante de la máquina. Los operadores siempre deben consultar el manual de la máquina y recibir la capacitación adecuada antes de operar la cizalla.
4. Capacidad y precisión de corte
La capacidad de corte y la precisión son consideraciones importantes cuando se usa una cizalla. Analicemos cada uno de ellos:
Capacidad de corte:
(1) Las cizallas tienen una capacidad de corte específica, que se refiere al grosor y ancho máximos del material que se puede cortar de manera efectiva. La capacidad de corte está determinada por factores como la potencia de la máquina, la fuerza de las cuchillas y la rigidez de la mesa de corte.
(2) Es crucial elegir una cizalla con una capacidad de corte que coincida con los requisitos de los materiales con los que trabajará. Intentar cortar materiales más allá de la capacidad de la máquina puede provocar una mala calidad de corte, daños en la hoja o incluso un mal funcionamiento de la máquina.
Precisión de corte:
(1) La precisión de corte se refiere a la capacidad de la cizalla para realizar cortes precisos y uniformes. Está influenciado por varios factores, incluidos el diseño y el estado de la máquina, el afilado y la alineación de las cuchillas y los sistemas de control y seguimiento.
(2) Para lograr una alta precisión de corte, es importante mantener la cizalla correctamente. El afilado y el reemplazo regulares de las hojas, así como el mantenimiento y la calibración de rutina, pueden ayudar a garantizar cortes precisos.
(3) La habilidad y la experiencia del operador también juegan un papel importante para lograr la precisión de corte. El posicionamiento adecuado del material, el ajuste de la holgura de la hoja y el control cuidadoso del proceso de corte son esenciales para obtener cortes precisos y limpios.
Factores que afectan la precisión:
(1) Condición de la hoja: las hojas desafiladas o dañadas pueden provocar cortes desiguales y una precisión reducida. La inspección y el mantenimiento regulares de las cuchillas son necesarios para mantener la precisión de corte.
(2) Espacio libre de la hoja: El espacio libre incorrecto de la hoja puede resultar en cortes distorsionados o incompletos. Es importante establecer la holgura adecuada de la hoja para el material que se está cortando.
(3) Alineación del material: la alineación adecuada del material con la mesa de corte y el tope trasero es fundamental para realizar cortes precisos. La desalineación puede causar cortes torcidos o desiguales.
(4) Rigidez de la máquina: la rigidez de la cizalla, incluida la mesa de cizalla y el marco, afecta la precisión del corte. Una máquina robusta y bien mantenida proporciona una mejor estabilidad y reduce las posibilidades de desviación durante el proceso de corte.
Se recomienda seguir las pautas y recomendaciones del fabricante para la cizalla específica que se utilice. El mantenimiento regular, la inspección de la hoja y la capacitación del operador son esenciales para garantizar una capacidad y precisión de corte óptimas.
5.Consideraciones de seguridad
Las consideraciones de seguridad son de suma importancia cuando se opera una cizalla. Aquí hay algunas medidas de seguridad clave a tener en cuenta:
(1) Lea y siga el manual: familiarícese con las instrucciones del fabricante y las pautas de seguridad proporcionadas en el manual de la máquina. Comprenda las características, los controles y los peligros potenciales de la máquina antes de operarla.
(2) Equipo de Protección Personal (EPP): Siempre use el EPP adecuado, incluidos anteojos o gafas de seguridad, guantes y protección para los oídos. Según la máquina específica y los materiales que se corten, es posible que se requiera equipo de protección adicional, como un protector facial o un delantal.
(3) Inspección de la máquina: antes de poner en marcha la máquina, inspecciónela para detectar cualquier signo de daño, piezas sueltas o componentes que no funcionen correctamente. Asegúrese de que todas las protecciones y dispositivos de seguridad estén en su lugar y funcionen correctamente.
(4) Capacitación y competencia: solo el personal capacitado y autorizado debe operar una máquina cortadora. La capacitación adecuada debe cubrir la operación de la máquina, los procedimientos de seguridad, el apagado de emergencia y el manejo de materiales.
(5) Manipulación de materiales: tenga cuidado al manipular materiales, especialmente los grandes o pesados. Use equipo de elevación o asistencia cuando sea necesario para evitar tensión o lesiones.
(6) Parada de emergencia: familiarícese con la ubicación y el funcionamiento del botón o interruptor de parada de emergencia. Esté preparado para usarlo en caso de cualquier emergencia o situación insegura.
(7) Seguridad de las cuchillas: nunca toque el área de corte mientras la máquina está en funcionamiento ni intente ajustar las cuchillas sin la capacitación adecuada. Siempre espere a que la máquina se detenga por completo antes de realizar cualquier ajuste o mantenimiento.
(8) Limpieza: Mantener un área de trabajo limpia y organizada. Quite los desechos, desechos u obstrucciones que puedan interferir con el funcionamiento de la máquina o causar accidentes.
(9) Bloqueo/etiquetado: siga los procedimientos adecuados de bloqueo/etiquetado al realizar tareas de mantenimiento o reparación en la máquina. Esto implica desconectar la fuente de alimentación y asegurarse de que no se pueda volver a activar accidentalmente.
(10) Mantenimiento regular: Respete el programa de mantenimiento recomendado para la cizalla. Esto incluye el afilado de cuchillas, la lubricación y la inspección de componentes mecánicos y eléctricos.
Recuerde, la seguridad siempre debe ser la máxima prioridad al operar cualquier maquinaria. Si tiene alguna inquietud o encuentra algún problema con la cizalla, detenga la operación de inmediato y busque ayuda de un técnico o supervisor calificado.
Máquina de corte por láser:
1. Introducción al corte por láser:
El corte por láser es un método altamente preciso y versátil para cortar diversos materiales utilizando un rayo láser de alta potencia. Ha revolucionado la industria manufacturera al proporcionar una alternativa más rápida, precisa y eficiente a los métodos de corte tradicionales. Las máquinas de corte por láser se utilizan en una amplia gama de industrias, incluidas la automotriz, aeroespacial, electrónica, señalización y fabricación de joyas.
El corte por láser funciona dirigiendo un rayo láser sobre el material a cortar. El rayo láser es generado por un resonador láser, que consta de un medio láser (como CO2, fibra o cristales dopados con neodimio) y un sistema para excitar el medio láser (como descarga eléctrica o bombeo de diodos). Luego, el rayo láser se enfoca en el material usando una serie de espejos y lentes, lo que aumenta la intensidad del rayo. El intenso calor del rayo láser derrite, quema o vaporiza el material, creando un corte limpio y preciso.
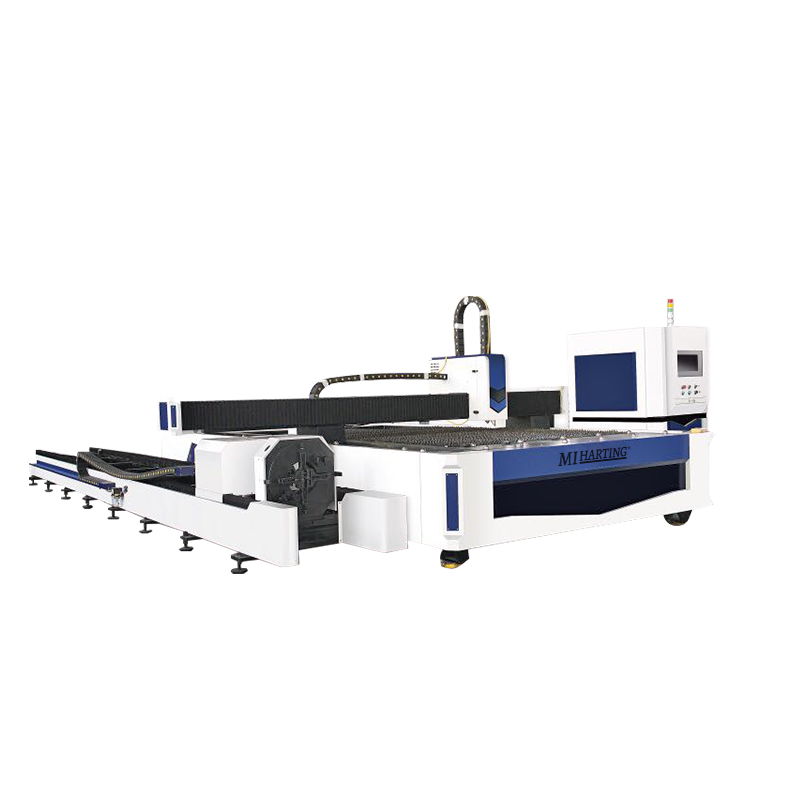
2. Tipos de máquinas de corte por láser:
Hay diferentes tipos de máquinas de corte por láser disponibles, cada una con sus propias ventajas y aplicaciones adecuadas. Los tipos más comunes incluyen láseres de CO2, láseres de fibra y láseres de neodimio.
Los láseres de CO2 son el tipo de máquina de corte por láser más utilizado. Utilizan una mezcla de dióxido de carbono, nitrógeno y helio como medio láser. Los láseres de CO2 son versátiles y pueden cortar una amplia gama de materiales, incluidos materiales no metálicos como plásticos, madera y telas, además de metales.
Los láseres de fibra utilizan fibras ópticas como medio láser. Son altamente eficientes y se utilizan principalmente para cortar metales, incluidos acero inoxidable, aluminio y cobre. Los láseres de fibra ofrecen una alta calidad de haz, lo que se traduce en velocidades de corte más rápidas y una mayor precisión.
Los láseres de neodimio utilizan cristales dopados con neodimio (como granate de itrio y aluminio dopado con neodimio o Nd: YAG) como medio láser. Son conocidos por su alta energía y se utilizan para corte y grabado de precisión. Los láseres de neodimio se usan comúnmente en aplicaciones que requieren alta potencia y detalles finos, como la fabricación de joyas y el micromecanizado.
3.Ventajas y limitaciones:
El corte por láser ofrece varias ventajas sobre los métodos de corte tradicionales. Una de las principales ventajas es su alta precisión y exactitud. Las máquinas de corte por láser pueden lograr cortes intrincados y complejos con una distorsión mínima. También proporcionan una excelente calidad de borde, eliminando la necesidad de procesos de acabado adicionales.
Otra ventaja es la velocidad y eficiencia del corte por láser. Las máquinas de corte por láser pueden cortar a altas velocidades, lo que resulta en tiempos de producción más rápidos y una mayor productividad. También pueden cortar múltiples partes simultáneamente, mejorando aún más la eficiencia.
El corte por láser es un método de corte sin contacto, lo que significa que no hay contacto físico entre la herramienta de corte y el material. Esto reduce el riesgo de dañar el material y permite cortar materiales delicados o frágiles.
Sin embargo, el corte por láser tiene algunas limitaciones. La capacidad de espesor de una máquina de corte por láser depende de la potencia del láser y del tipo de material que se corta. Los materiales más gruesos pueden requerir varias pasadas o un láser más potente para lograr un corte limpio. Además, las máquinas de corte por láser pueden ser costosas de comprar y mantener, lo que las hace más adecuadas para entornos de producción de alto volumen.
4. Compatibilidad de materiales y grosor:
Las máquinas de corte por láser pueden cortar una amplia gama de materiales, incluidos metales, plásticos, madera, textiles y más. La compatibilidad de un material con el corte por láser depende de su capacidad para absorber la energía del láser. Los materiales que son altamente reflectantes, como el cobre o el aluminio, pueden requerir una mayor potencia de láser para el corte.
El grosor del material que se puede cortar depende de la potencia del láser y del tipo de material. Las máquinas de corte por láser normalmente pueden cortar materiales delgados con alta precisión. Por ejemplo, una máquina de corte por láser de CO2 puede cortar acero de hasta 25 mm de espesor, mientras que una máquina de corte por láser de fibra puede cortar acero de hasta 30 mm de espesor. Sin embargo, la capacidad máxima de espesor puede variar según la máquina específica y la potencia del láser.
Es importante considerar la compatibilidad del material y la capacidad de espesor de una máquina de corte por láser antes de seleccionar la máquina adecuada para una aplicación específica. Consultar con un proveedor o fabricante de máquinas de corte por láser puede ayudar a determinar la mejor máquina para un requisito de material y espesor en particular.
Prensa de poder:
1.Explorando máquinas de prensas eléctricas:
Las prensas eléctricas, también conocidas como prensas o prensas de estampado, son máquinas versátiles que se utilizan en la metalurgia para diversas operaciones, como punzonado, doblado, conformado y troquelado. Se utilizan comúnmente en industrias como la automotriz, la fabricación, la construcción y la producción de electrodomésticos. Las máquinas de prensado eléctrico vienen en diferentes tamaños y configuraciones para adaptarse a diferentes aplicaciones y requisitos de producción.
Las máquinas de prensas eléctricas están diseñadas para aplicar fuerza a una pieza de trabajo mediante sistemas mecánicos o hidráulicos. Son capaces de ejercer una alta presión para dar forma, cortar o formar láminas de metal u otros materiales. Las máquinas de prensas eléctricas se pueden clasificar en tipos mecánicos e hidráulicos según su fuente de energía y operación.
2. Prensa mecánica vs. hidráulica:
Las prensas mecánicas utilizan fuerza mecánica, generalmente generada por un volante y un cigüeñal, para realizar operaciones. Son conocidos por su alta velocidad y productividad. Las máquinas de prensas mecánicas tienen un embrague mecánico o un sistema de frenos que controla la carrera y el movimiento de detención del ariete. Son adecuados para entornos de producción de alto volumen donde la velocidad y la precisión son importantes.
Las prensas hidráulicas, por otro lado, utilizan sistemas hidráulicos para generar fuerza. Utilizan cilindros hidráulicos para aplicar presión al ariete y realizar operaciones. Las prensas hidráulicas ofrecen más control y flexibilidad en términos de ajuste de fuerza y modulación de velocidad. A menudo se utilizan para operaciones que requieren un control preciso de la fuerza o para aplicaciones que involucran embutición profunda o formación de materiales.
La elección entre una prensa mecánica o hidráulica depende de los requisitos específicos de la aplicación. Se deben considerar factores como el tipo de operación, el grosor del material, el volumen de producción y los requisitos de precisión al seleccionar la máquina de prensa mecánica adecuada.
3. Componentes y funcionamiento:
Las máquinas de prensas eléctricas constan de varios componentes clave que trabajan juntos para realizar diversas operaciones. Estos componentes incluyen el marco, la corredera o el ariete, el refuerzo, la matriz, el sistema de embrague o freno y el sistema de control.
El bastidor proporciona la estructura y el soporte de la máquina. Por lo general, está hecho de hierro fundido o acero para soportar las fuerzas ejercidas durante la operación. La corredera, también conocida como ariete, se mueve hacia arriba y hacia abajo para aplicar fuerza al material. Es guiado por el marco y puede ser accionado por un cigüeñal o cilindros hidráulicos.
El cabezal es una superficie plana sobre la que se coloca el material. Proporciona soporte a la pieza de trabajo durante la operación. El troquel es una herramienta de forma especial que realiza la operación deseada, como perforar un agujero o doblar una hoja de metal. El troquel se monta en el cabezal o en el carnero, según el tipo de operación.
El sistema de embrague o freno controla la carrera y el movimiento de frenado del ariete. En las prensas mecánicas, se utiliza un embrague o freno mecánico para activar o desactivar el volante, controlando el movimiento del ariete. En las prensas hidráulicas, el sistema hidráulico controla el movimiento del ariete.
El sistema de control de una máquina de prensa eléctrica puede variar según la máquina específica y sus características. Puede variar desde simples controles manuales hasta sistemas avanzados de control numérico por computadora (CNC). Los sistemas CNC ofrecen un control preciso sobre el funcionamiento de la máquina, lo que permite procesos programables y repetibles.
4. Capacidades de punzonado, doblado y conformado:
Las máquinas de prensas eléctricas son capaces de realizar varias operaciones, dependiendo de las herramientas y los troqueles utilizados. Algunas operaciones comunes incluyen punzonado, doblado, conformado, troquelado, acuñado, estampado y embutición profunda.
El punzonado es un proceso de creación de agujeros o formas en un material utilizando un juego de punzones y matrices. La flexión es el proceso de deformar un material para formar ángulos o curvas. La formación implica dar forma a un material para crear objetos tridimensionales o geometrías complejas. El corte en blanco es el proceso de cortar una forma plana de una pieza más grande de material. La acuñación es un proceso que consiste en comprimir un material para crear una forma o patrón preciso. El repujado es el proceso de crear relieves o depresiones
Conclusión:
Al profundizar en el conocimiento integral proporcionado en esta guía definitiva, ha adquirido una comprensión sólida de Prensa plegadora, herramientas de plegadora, cizalla, máquina de corte por láser y prensa eléctrica. Armado con este conocimiento, puede seleccionar, operar y optimizar con confianza estas máquinas para lograr resultados de fabricación de metal precisos y eficientes. Recuerde priorizar la seguridad, el mantenimiento regular y mantenerse actualizado con los últimos avances en la industria para mantenerse a la vanguardia en el mundo en constante evolución de la metalurgia.
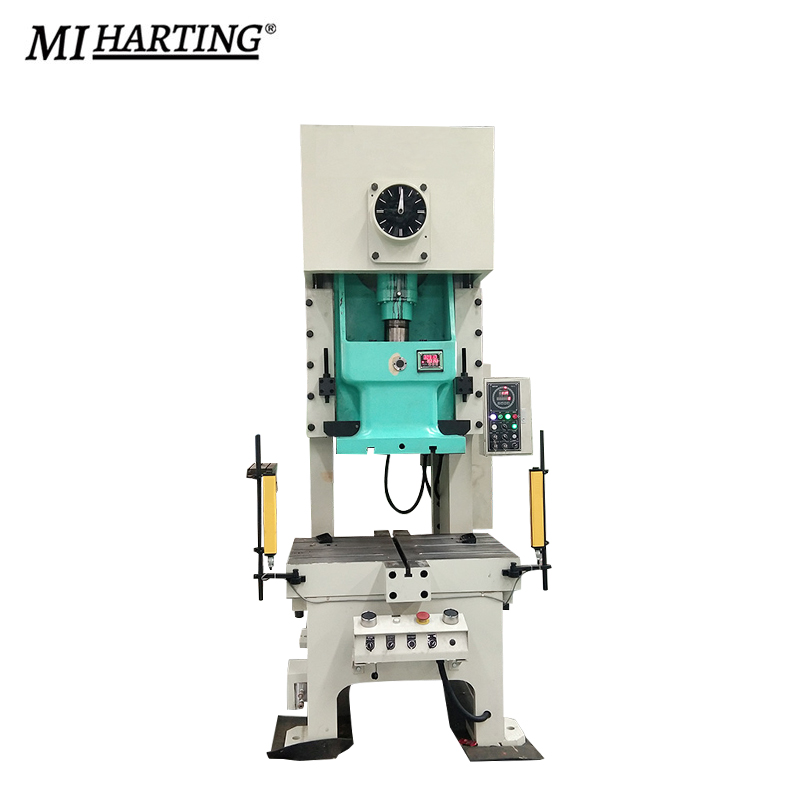