Introduction:
Sheet metal bending is a fundamental process in the manufacturing industry that involves reshaping flat metal sheets into desired angles and shapes. This article aims to provide an overview of how sheet metal bending works, including the techniques, tools, and factors that influence the bending process.
The Basics of Sheet Metal Bending:
Sheet metal bending involves the application of force to deform a metal sheet along a straight axis, creating a bend. The bending operation typically occurs between a punch and a die, with the metal sheet placed in between. The punch applies downward force, while the die provides support and defines the bending angle.
Types of Bending Techniques:
There are several common bending techniques used in sheet metal fabrication:
a. V-Bending: In this technique, a V-shaped punch and matching die are used to create a bend. The depth of the V-shaped groove determines the bending angle.
b. U-Bending: U-bending involves using a U-shaped punch and die to form a rounded bend. This technique is often used for creating curved or tubular shapes.
c. Air Bending: Air bending utilizes a single V-shaped punch and die, where the punch does not fully contact the workpiece. The bending angle is determined by controlling the depth of penetration.
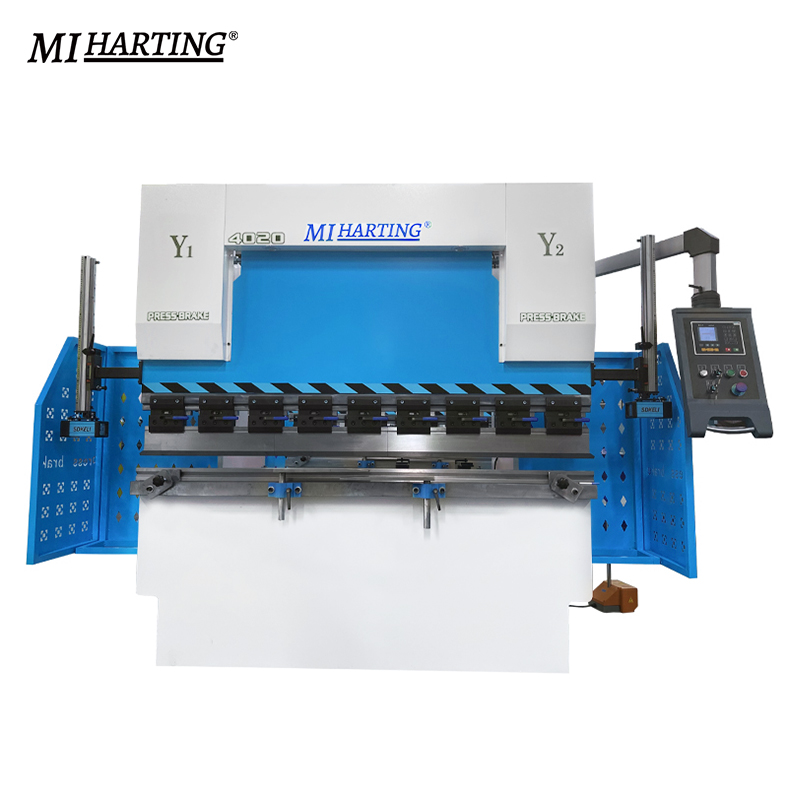
Factors Influencing the Bending Process:
Several factors impact the outcome of sheet metal bending:
a. Material Selection: Different metals have varying degrees of ductility, which affects their ability to be bent without cracking or deformation. Commonly used materials for bending include aluminum, steel, and stainless steel.
b. Thickness and Grain Orientation: The thickness of the metal sheet plays a crucial role in determining the required force for bending. Additionally, the direction of the grain within the sheet affects its ability to bend smoothly.
c. Bend Radius and Angle: The radius of the bend determines its sharpness, while the bending angle defines the final shape. Both factors are integral to achieving the desired form and functionality of the bent component.
Tools Used in Sheet Metal Bending:
To execute the bending process effectively, various tools are utilized:
a. Press Brake: A press brake is the primary machine used for sheet metal bending. It consists of a hydraulic or mechanical press that applies force to the workpiece, along with a set of punches and dies to create the desired bends.
b. Gauges and Fixtures: Gauges and fixtures aid in accurately positioning the metal sheet and ensuring consistent bends throughout the production process.
Quality Control and Post-Bending Processes:
To ensure high-quality bent components, manufacturers perform quality control measures such as inspecting the bends for accuracy, checking for cracks or deformations, and verifying dimensional tolerances. Additionally, post-bending processes like trimming, deburring, and surface finishing may be carried out to refine the final product.
Conclusion:
Sheet metal bending is a crucial process in the manufacturing industry, enabling the creation of complex and functional components. Understanding the basics of sheet metal bending, including the techniques, tools, and influencing factors, allows manufacturers to optimize the process for improved efficiency, precision, and quality. With the right equipment and expertise, sheet metal bending can be executed with precision, meeting the diverse needs of various industries.