Mechanical Punch Press Production Line Standard Configuration
Parameters | Unit | J21S-16 | J21S-25 | J21S--40 | J21S-63 | J21S-80 | J21S-100 | J21S-125 | J21S-160 | J21S-200 | J21S-250 | |
Nominal Force | Kn | 160 | 250 | 400 | 630 | 800 | 1000 | 1250 | 1600 | 2000 | 2500 | |
Stroke of Nominal force | mm | 2 | 3 | 5 | 5 | 6 | 6 | 8 | 8 | 10 | 14 | |
Slider stroke | mm | 60 | 70 | 100 | 100 | 120 | 130 | 130 | 160 | 180 | 200 | |
Slip an piece of itinerary time | Time/min | 110 | 60 | 55 | 50 | 45 | 43 | 35 | 28 | 28 | 28 | |
Maximum closed height | mm | 190 | 210 | 325 | 350 | 370 | 380 | 400 | 400 | 420 | 430 | |
Closed height adjustment | mm | 40 | 50 | 65 | 80 | 90 | 100 | 110 | 120 | 120 | 130 | |
Distance from slider block centre to the frame | mm | 500 | 500 | 500 | 500 | 500 | 710 | 710 | 800 | 800 | 800 | |
Length between columns | mm | 160 | 230 | 270 | 310 | 410 | 520 | 560 | 580 | 680 | 700 | |
Hole size for die handle | Diameter | mm | 35 | 40 | 40 | 50 | 60 | 60 | 70 | 80 | 90 | 100 |
Depth | mm | 60 | 60 | 70 | 70 | 70 | 90 | 120 | 150 | 150 | 170 | |
Size of worktable | Left-right | mm | 440 | 500 | 680 | 720 | 750 | 900 | 930 | 1140 | 1390 | 1500 |
Front-back | mm | 270 | 32 | 460 | 480 | 530 | 630 | 630 | 740 | 820 | 900 | |
Blanking hole diameter | mm | 100 | 130 | 150 | 160 | 180 | 180 | 200 | 200 | 220 | 250 | |
Table plate thickness | mm | 40 | 50 | 65 | 80 | 100 | 120 | 130 | 150 | 150 | 150 | |
Dimensions | Left-right | mm | 750 | 950 | 1080 | 1150 | 1370 | 1510 | 1600 | 1890 | 2035 | 2360 |
Front-back | mm | 1330 | 1520 | 1695 | 1720 | 1985 | 2235 | 2250 | 2480 | 2895 | 3095 | |
Height | mm | 1750 | 2040 | 2350 | 2450 | 2670 | 2750 | 2850 | 2920 | 3780 | 3850 | |
Power | kw | 1.5 | 2.2 | 4 | 5.5 | 7.5 | 11 | 11 | 15 | 18.5 | 22 |
Punch Press Production Line Detailed Images
•Steel welded frame with high rigidity.
•Motor with inverter.
•Combined wet friction clutch.
•Rectangular hexahedron lengthened guide; OCP-315/400 with octahedral lengthened guide.
•Hydraulic overload protector.
•Lifting balance cylinder.
•Imported dual solenoid valve.
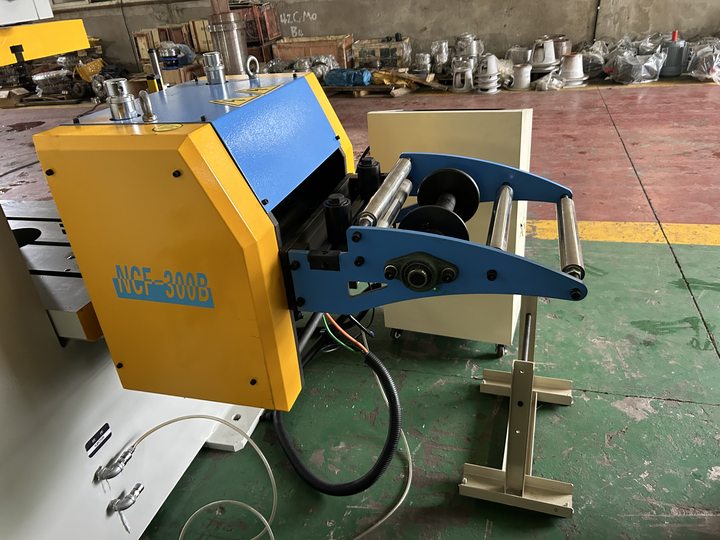
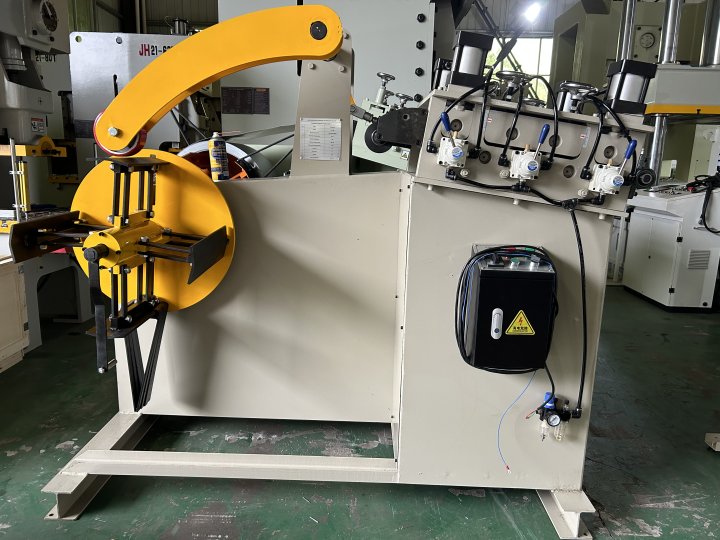
•Forced grease lubrication.
•Balance cylinder: manual oil lubrication.
•Integrated panel (elec.com included).
•PLC control of international brand.
•Contactor and button of international brand.
•CE safety specifications
•Optional: air cushion, light curtain, automotive device.
Mechanical Punch Press Production Line Information
Name | Punch press production line |
Customization | Support machine color, model, and system customization |
Main and auxiliary equipment | - Feeder - Leveling machine - Punching machine - Recycling machine |
Characteristic | Fully automated processing from raw materials to finished products |
Punch Production Line Mold And Material Selection
Mold material selection Chromium steel (Cr12, Cr12MoV, CrWMn) Features: high hardness, good wear resistance, suitable for ordinary stamping parts, and is the most commonly used stamping die material in China.
Tool steel (such as SKD11, DC53) Features: Excellent comprehensive performance (hardness 58-62HRC), high cost performance, suitable for precision stamping and complex molds.
Carbide (such as YG series) Features: Ultra-high hardness and wear resistance, suitable for processing hard materials such as stainless steel and high carbon steel, but the cost is high.
High speed steel (such as W6Mo5Cr4V2) Features: High temperature resistance, wear resistance, suitable for high-precision cutting processes, but expensive, mostly used in high-end fields |
Stamping material adaptation
Aluminum/galvanized sheet Applicable molds: tool steel or chromium steel. Pay attention to mold gap adjustment to reduce burrs.
Stainless steel/high carbon steel Applicable molds: carbide or high-speed steel, the wear resistance of the mold needs to be improved.
Thin plate (≤3mm) Applicable molds: low alloy tool steel (reduces quenching deformation) or detachable stripper plate design |
Punch Press Production Line Advantages
Production efficiency improvement and product quality assurance
- The power press machine reduces equipment waiting time by optimizing the program, directly increasing the stamping speed, and the production cycle can reach more than 30 times/minute. The servo stamping line can also achieve 24-hour uninterrupted operation, and cooperate with the automated feeding system to significantly shorten the production cycle.
- The precision-controlled servo hydraulic press machine can stop and maintain pressure at any position. Combined with CNC stretching pad technology, it ensures the forming accuracy of stamping parts (such as car covering parts without burrs and accurate dimensions). Modular flexible lines monitor and correct quality defects in real time by integrating visual inspection and online measurement systems.
Flexibility and adaptability
- Compatible with multiple varieties and small batches
The flexible punch press production line achieves "multiple outputs on one machine" through quick mold replacement (fully automatic mold storage rack and adjustment device) to adapt to the diverse needs of the market - Complex process support
The stamping robot supports single-axis or multi-axis linkage to complete linear, circular, irregular curve and other motion trajectories, and is suitable for complex forming processes such as high-strength steel and new materials.
Significant cost-effectiveness
- Labor cost savings
A single punching press production line requires only 1-2 people to monitor, which reduces manpower input by more than 70% compared to traditional production lines and avoids the risk of labor fluctuations. - Energy consumption and material optimization
The servo hydraulic power press has an energy recovery function, combined with a modular design to reduce equipment idleness and reduce energy consumption by 30%-50%.
Green and environmentally friendly manufacturing
Use energy-saving equipment and waste recycling technology (such as waste recycling rate exceeding 90%) to reduce carbon emissions and industrial pollution Summary
The punch press production line achieves the comprehensive goals of high efficiency, high precision, low cost and green production through automation, intelligence and flexibility technology. It is especially suitable for industries with high mass production and quality requirements such as automobiles, electronics and home appliances.
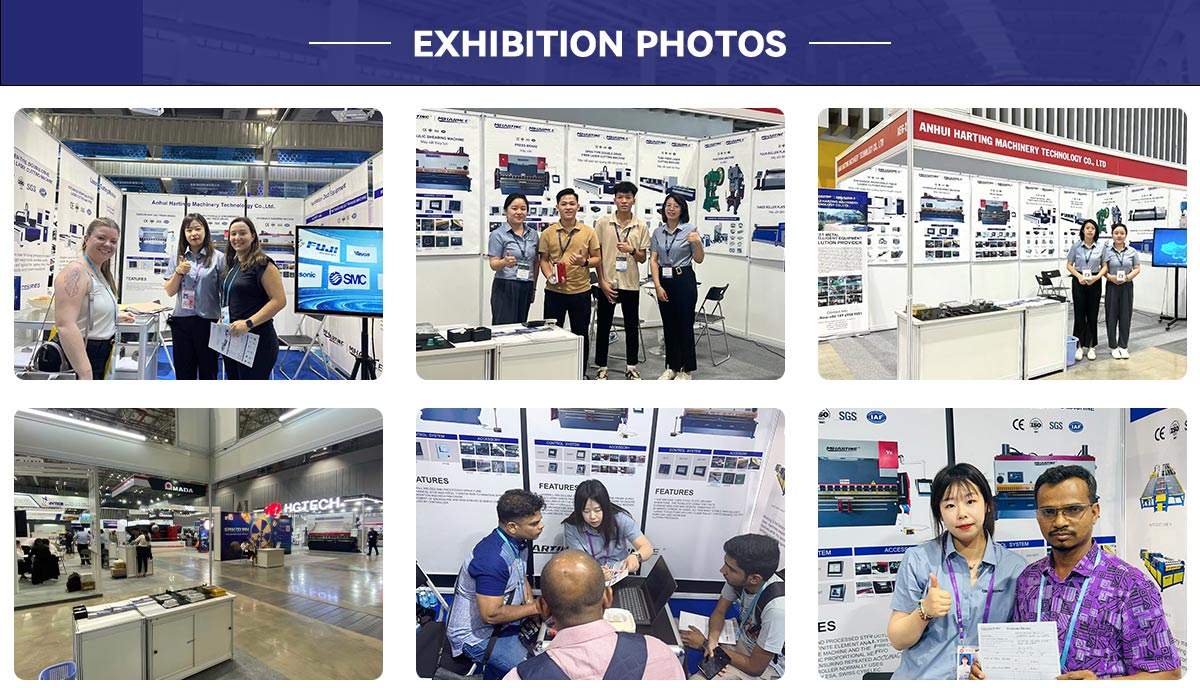
Punch Press Production Line Attention
Key points for mold selection
Reasonable mold clearance
If the gap is too large, it will easily produce burrs, while if it is too small, it will accelerate wear. For example: low carbon steel recommends a gap of 20% of plate thickness, and stainless steel requires 25-30%.
Matching processing needs
Mass production: Prioritize carbide or high-speed steel to extend mold life.
Complex shapes: Choose SKD11 or DC53 with good toughness.
Workstation and size optimization
The punching diameter matches the work station (for example, if φ12.7-31.7mm is selected, B station is selected) to avoid mold overload.
Mechanical Punch Press Production Line Maintenance and optimization suggestions
Regular maintenance: clean the mold, check the edge wear, and sharpen or replace it in time.
Process arrangement: Holes in the same process are processed together, crimping first and then punching to reduce material deformation.
Automation integration: equipped with feeding detection and pre-cutting devices to improve accuracy and efficiency