A manual bending machine and a CNC-controlled bending machine are both commonly used metalworking equipment, widely applied in the bending of materials such as steel and aluminum alloys. Although they share the same basic function, there are significant differences in terms of operating precision, efficiency, and application range.
Difference in Operating Methods
- Manual Bending Machine: As the name suggests, a manual bending machine relies on human operation. The operator adjusts the machine's control lever, pressure plate, and handwheel to perform the bending process. The operator must manually set the bending angle, pressure, and depth. While the manual bending machine is simpler to control, it requires a high level of skill and experience from the operator, and the bending process can be influenced by human factors.
- CNC-Controlled Bending Machine: Unlike the manual machine, a CNC-controlled bending machine uses a computer numerical control (CNC) system to automate the bending process. The operator inputs a program or sets parameters, and the machine follows preset instructions to complete the bending automatically. The introduction of the CNC system significantly enhances the automation level, making the operation more convenient and precise.
Precision and Consistency
- Manual Bending Machine: Since the manual bending machine depends on human adjustments, its precision and consistency are often influenced by the operator’s experience and the accuracy of manual controls. Especially when multiple identical bends are required, manual operation may lead to cumulative errors.
- CNC-Controlled Bending Machine: CNC bending machines offer higher precision and can control the bending angle, position, and pressure accurately in every operation. Through programmed settings, CNC-controlled machines ensure consistent bending results, minimizing human error and guaranteeing high precision and quality.
Production Efficiency and Application Range
- Manual Bending Machine: Manual bending machines are suitable for small batch or simple bending tasks, and their operation is relatively simple. They are best for situations where high precision is not crucial. However, since manual intervention is required, production efficiency is lower, and they are not suitable for complex bending tasks.
- CNC-Controlled Bending Machine: CNC-controlled bending machines offer higher production efficiency. With pre-set programs and automated control, they significantly reduce manual labor time, especially in large-scale production and complex bending processes. For tasks that require high precision and variable processes, CNC bending machines are the ideal choice.
Equipment Cost and Maintenance
- Manual Bending Machine: The purchase cost of a manual bending machine is lower, and due to its simpler structure, maintenance and upkeep are relatively easy. It is suitable for small businesses or low-frequency processing needs with limited budgets.
- CNC-Controlled Bending Machine: CNC-controlled bending machines come with a higher purchase cost, requiring a larger investment. However, due to their high precision and efficiency, they can save on labor costs and increase production rates over time. Although maintenance costs may be higher for CNC equipment, their efficient operation can bring significant economic benefits over the long run.
Application Scenario Selection
- Manual Bending Machine: Best suited for small batch production, components that do not require high precision, and production environments with limited budgets. For example, small workshops or companies that need flexible customization might opt for manual bending machines.
- CNC-Controlled Bending Machine: Ideal for situations that require high precision and efficiency, especially in large-scale production. Industries such as automotive, aerospace, and home appliances, where large quantities of high-precision metal parts are required, would benefit from the stable performance and high-quality results provided by CNC-controlled bending machines.
Both manual and CNC-controlled bending machines have their advantages and are suitable for different production needs. If low-cost, simple operation, small production batches, and less stringent precision are required, a manual bending machine may be a good choice. However, if high precision, efficiency, and complex processes are desired, especially for large production volumes, the CNC-controlled bending machine is the more ideal option. Mihating is a professional high quality press brake equipment manufacturer and exporter in China. We have a variety of systems of bending machine equipment, welcome to discuss with us.
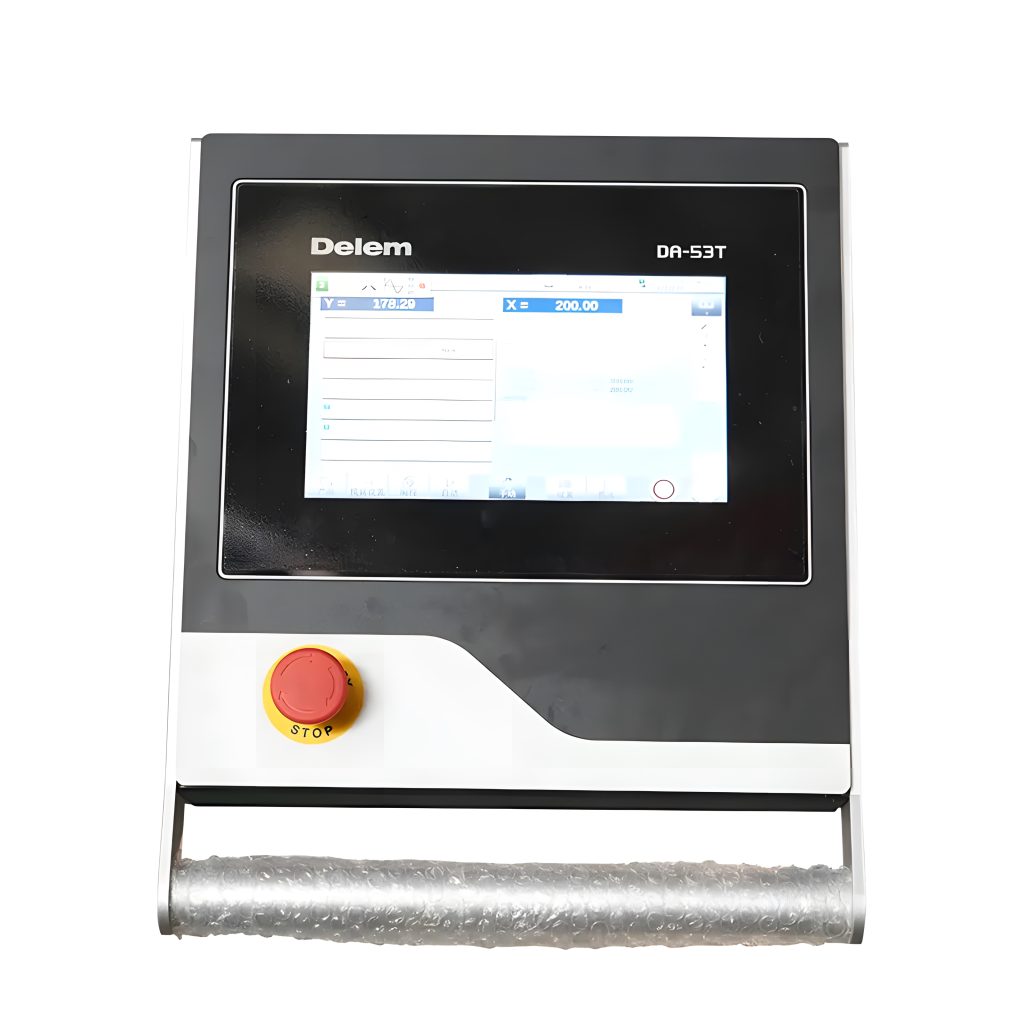
•"Shortcut" touch navigation. 10.1" high-definition TFT display •Multiple 4-axis control •Deflection compensation control •With mold/material/product library •Support servo or frequency conversion control •Advanced X-axis control method can control both loop adjustment and open-loop false adjustment. •Network dual-machine linkage (optional) •USB peripheral interface
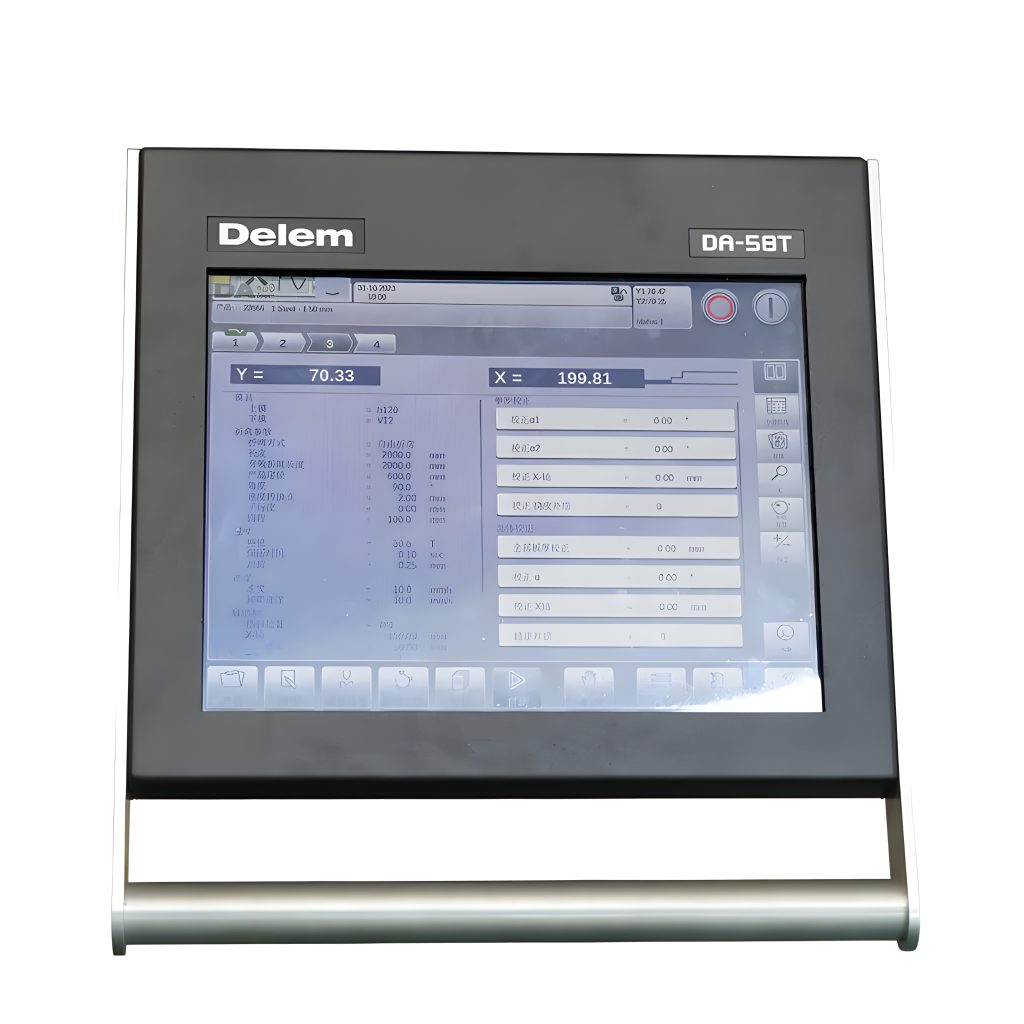
•2D touch graphics programming •15° high resolution TFT true color display •Bending process planning •Disturbance compensation control •Servo and inverter control modes •Advanced Y-axis control algorithm can control both closed-loop and open-loop. • USB port
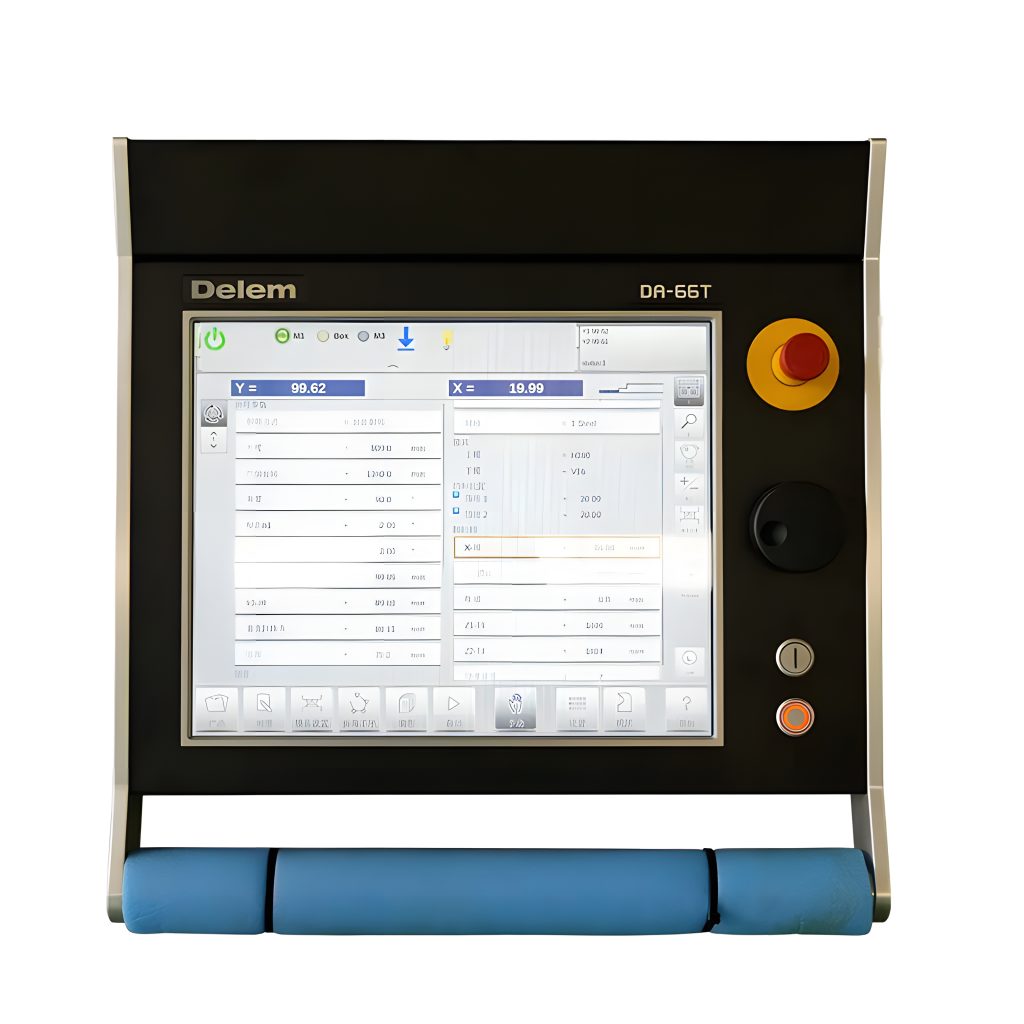
•2D touch graphics programming •3D product graphic simulation display •17" high resolution TFT true color display • COMPLETE WINDOWS APPLICATION PACKAGE •Compatible with DELEM modular structure system •USB, peripheral interface •User program application in multi-tasking environment •Angle detection sensor interface
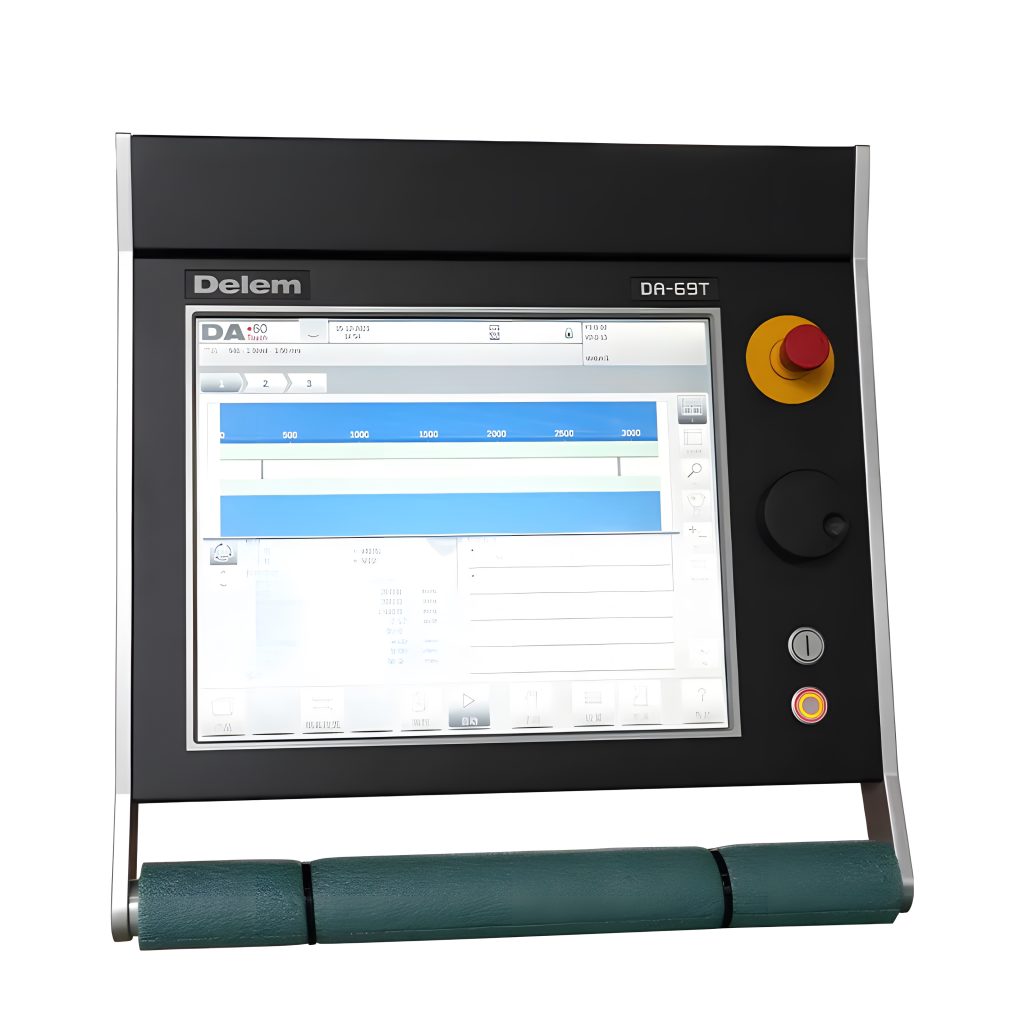
•2D and 3D touch graphics programming •30 product graphic simulation displays •17° high resolution TFT true color display •Compatible with DELEM modular structure system •USB, peripheral interface. •User program application in multi-tasking environment •Angle detection sensor interface
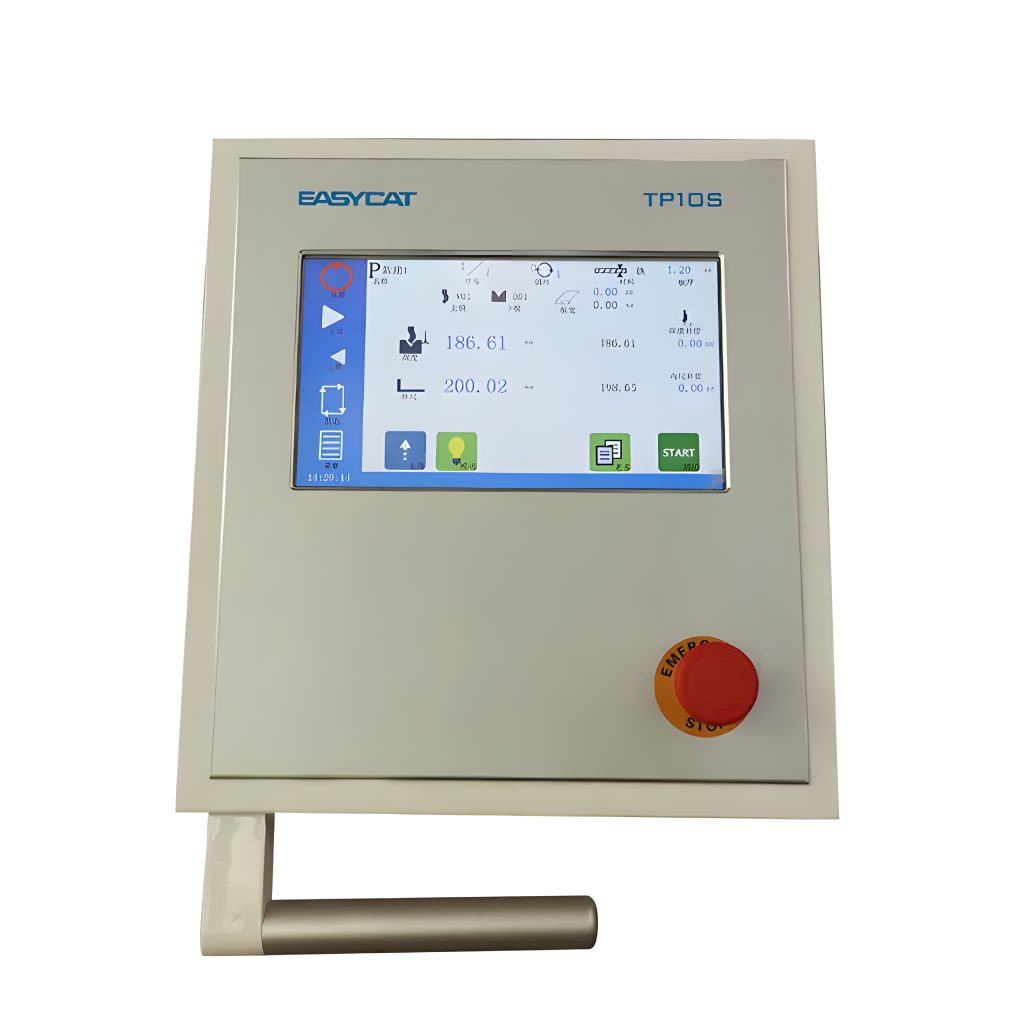
• Back gauge control • Control universal motors or inverters • Pressure holding and unloading time setting • Work piece count • Stores 40 programs with 25 steps each • Promotional features
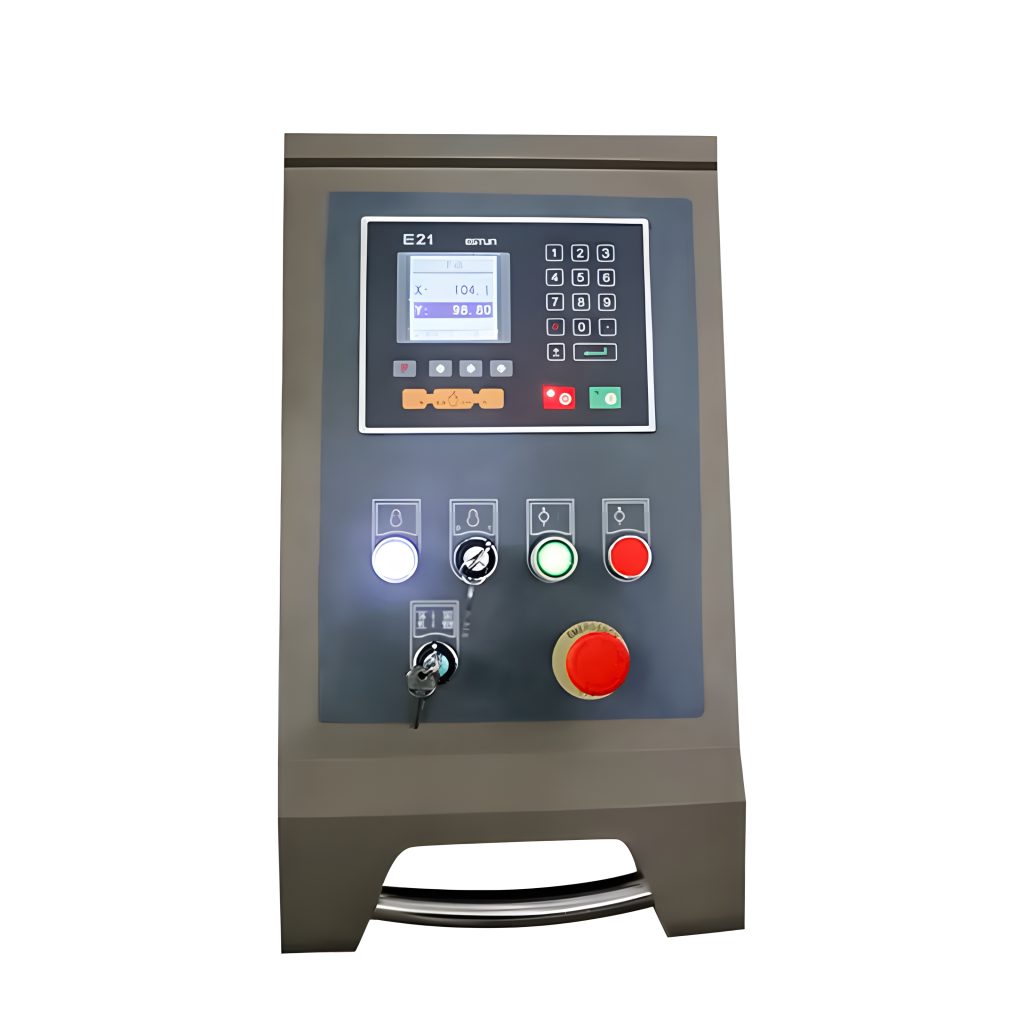
•Backgauge control •Control regular motors or inverters •Pressure holding and unloading time setting •Work piece count •Store 40 programs with 25 steps each •Preferential features